ЛАБОРАТОРНА РОБОТА № 8
ТЕРМІЧНА ОБРОБКА СТАЛЕЙ
Мета роботи: вивчення методики призначення режимів відпалу, нормалізації і гартування, придбання практичних навичок проведення різноманітних операцій термічної обробки, дослідження впливу вмісту вуглецю і температури відпуску на твердість загартованої сталі.
Матеріали та обладнання. Для виконання цієї лабораторної роботи надаються зразки сталей, термічна піч, термопара з приладом реєстрації температури, охолодні середовища (вода, мінеральне масло), прилади для вимірювання твердості.
Теоретичні відомості. Термічною обробкою сталі називається технологічний процес, який полягає в нагріванні сталі до певної температури, витримки і наступного охолодження з певною швидкістю. При термічній обробці отримують необхідні властивості сталі, змінюючи її структуру без зміни хімічного складу. Біля 40 % сталі, споживаної машинобудуванням для виготовлення деталей машин, приладів, устаткування, піддають різноманітним видам термічної обробки. Оскільки основними чинниками при термічній обробці є температура і час, то будь-який процес термічної обробки можна подати в цих координатах.
Основні параметри режиму термічної обробки - температура нагрівання (tН), швидкість нагрівання (vH), тривалість витримки при температурі нагрівання (tB) і швидкість охолодження (vo).
Температура нагрівання сплаву при конкретному виді термічної обробки визначається температурами фазових перетворень (критичними температурами) на відповідній діаграмі його стану. Ці критичні температури для кожної стадії позначаються літерою А з відповідним індексом ( А1, А2, А3, А4, Аcm). Критичні точки А1 на лінії PSK показують перетворення А ® П (при охолодженні – Аr1) або П ® А (при нагріванні – Аc1); А3 на лінії GS – початок виділення фериту з аустеніту при охолодженні або кінець його розчинення при нагріванні (відповідно – Аr3 і Ac3); Аст на лінії SE – початок виділення цементиту вторинного з аустеніту в заевтектоїдних сталях при охолодженні або кінець його розчинення при нагріванні (відповідно - Arcm і Accm).
Температура нагрівання при термічній обробці сталі, щоб уникнути її оплавлення, не повинна перевищувати лінії солідуса.
Швидкість нагрівання вибирається залежно від ряду чинників: теплопровідності сталі, форми і розмірів деталей, загальної маси деталей, що нагріваються, характеру їх розташування в печі та деяких інших.
Тривалість витримки при заданій температурі нагрівання визначається швидкістю фазових перетворень, що відбуваються в металі. Витримка необхідна для завершення фазових перетворень і вирівнювання температури по об’єму деталі.
Швидкість охолодження обирається залежно від ступеня стійкості переохолодженого аустеніту, обумовленого переважно хімічним складом сталі, а також від необхідних структури і властивостей сплаву. Залежно від швидкості охолодження вуглецевої сталі можуть бути отримані перлітна, сорбітна, троститна або мартенситна структури (рис. 8.1) з різноманітними властивостями.
Термічна обробка поділяється на власне термічну, хіміко-термічну і деформаційно-термічну. Перша в свою чергу включає чотири основні групи: відпал першого роду, відпал другого роду, гартування, відпуск.
В і д п а л (annealing) п е р ш о г о р о д у сприяє усуненню відхилень у структурі сплавів від рівноважного стану, що виникли при литті, деформуванні, механічній обробці, зварюванні й інших технологічних процесах. Розрізняють такі основні види відпалу першого роду: дифузійний, рекристалізаційний, низький.
Дифузійний, або гомогенізувальний, відпал застосовується для усунення ліквації, тобто неоднорідності хімічного складу всередині окремих зерен або в об’ємі сплаву, що виникає частіше всього в процесі кристалізації. Він полягає у нагріванні сталі до температур, що значно перевищують критичні (1050 ... 1200 °С), тривалій витримці (10 ... 100 год) і повільному охолодженні (з виключеною піччю), що забезпечує дифузію нерівномірно розподілених елементів.
Для усунення різноманітних відхилень у структурі сплавів від рівноважного стану, що виникли в результаті наклепу при холодному пластичному деформуванні, застосовується рекристалізаційний відпал. Він включає нагрівання металу до температур, що перевищують температуру рекристалізації (для сталі Трекр = 0,3 ... 0,4 Тпл), витримку (1 ... 2 год) і повільне охолодження.
Низький відпал застосовується для усунення залишкових внутрішніх напружень, що виникають, наприклад, у зоні термічного впливу при зварюванні виробів внаслідок нерівномірного охолодження виливків або зрізання окремих об’ємів металу при механічній обробці і порушення врівноважених напружень між окремими частинами деталі. Він включає нагрівання металу до температур 150 ... 700°С, витримку і наступне повільне охолодження.
В і д п а л д р у г о г о р о д у (фазова перекристалізація) – термічна обробка, що включає нагрівання сталі до температур, що перевищують Аc1 або Ac3, витримку і повільне охолодження, що має за мету забезпечення фазових перетворень і досягнення практично рівноважних (відповідно до діаграми стану системи Fe – Fe3C) фазового і структурного станів. Після відпалу структура сталей така: доевтектоїдних – Ф + П, евтектоїдних – П; заевтектоїдних – П + ЦІІ. Оскільки такий відпал забезпечує мінімальну твердість і найкращу оброблюваність сталі різанням, як правило, він є підготовчою термічною обробкою перед обробкою різанням. Проте в деяких випадках (наприклад, для крупних виливків) він може бути й остаточним видом обробки. Розрізняють такі основні види відпалу другого роду: повний, неповний, нормалізаційний, ізотермічний.
При повному відпалі сталь нагрівають до температури, що на 20 ... 30 °С перевищує Ac3, витримують при цій температурі, повільно охолоджують до 500 ... 600 °С разом із піччю, а потім на повітрі. Повний відпал забезпечує повну фазову перекристалізацію і застосовується, як правило, для доевтектоїдних сталей з метою усунення дефектів структури (крупнозернистої, відманштетової тощо).
При неповному відпалі температура нагрівання сталі на 20 ... 30 °С вище Аc1, але не перевищує Ac3 або Accm. Після витримки сталь повільно охолоджують разом із піччю. При нагріванні відбувається часткова (неповна) перекристалізація сталі (в початковій структурі Ф + П або П + ЦІІ, при нагріванні тільки перліт перетворюється в аустеніт). Неповний відпал, проведений для заевтектоїдних сталей, називають сфероїдизацією. Він дозволяє одержувати сталь із структурою зернистого перліту. Така сталь має більш низьку твердість, вищу пластичність і кращу оброблюваність різанням, ніж сталь із пластинчастим перлітом. Для доевтектоїдних сталей неповний відпал також застосовують з метою покращення оброблюваності різанням.
Нормалізаційний відпал (нормалізація) включає нагрівання доевтектоїдної сталі до температури на 30 ... 50 °С вище Ac3, а заевтектоїдної – на 30 ... 50 °С вище Accm, ізотермічну витримку й охолодження на спокійному повітрі. Прискорене охолодження при нормалізації дозволяє отримати більш дисперсну (здрібнену) структуру сталі, що призводить до підвищення її твердості та міцності порівняно зі сталлю, що піддавалась повному відпалу. Оскільки температури нагрівання під нормалізацію порівняно високі, то для уникнення значного зростання зерна металу витримка повинна бути мінімальною, але забезпечувати рівномірний прогрів виробу по всьому перерізу.
Нормалізацією усувається цементитна сітка в заевтектоїдних сталях при підготовці їх до гартування. З огляду на більш високу продуктивність нормалізації порівняно з повним або неповним відпалом, їх часто заміняють нею при підготовці вуглецевих сталей до механічної обробки.
Ізотермічний відпал включає нагрівання сталі до температури, що на 30 ... 50 °С перевищуює Ас3, витримку, а потім перенос деталі в іншу піч із заданою температурою (нижче А1) і ізотермічну витримку її до повного розпаду аустеніту. Ізотермічний відпал покращує оброблюваність різанням і застосовується для деталей і заготівок невеликих розмірів.
Г а р т у в а н н я (heat strengthening) – термічна обробка, що включає нагрівання сталі вище критичних температур, ізотермічну витримку і наступне охолодження зі швидкістю вище критичної (vкр).
Під к р и т и ч н о ю ш в и д к і с т ю г а р т у в а н н я (critical speed of heat strengthening) розуміють мінімальну швидкість охолодження, що забезпечує бездифузійне перетворення аустеніту в мартенсит. Мета гартування – підвищення твердості, міцності і зносостійкості сталі. Змінюючи швидкість охолодження нагрітих сталей, що мають аустенітну структуру, і варіюючи тим самим ступінь переохолодження, можна одержувати сталі з різноманітною структурою і властивостями (рис. 8.1).
Так, при невеликих швидкостях охолодження (V1, V2, V3) в інтервалі температур 720 ... 550 °С з аустеніту утворюються пластинчасті ферито-цементитні суміші (перліт, сорбіт або троостит). В міру збільшення швидкості охолодження дисперсність суміші, нерівновісність структури сталі, а отже, її твердість і міцність зростають. При охолодженні зі швидкістю вище критичної (> V5) з аустеніту утвориться мартенсит, що є пересиченим твердим розчином проникнення вуглецю в ґратку a-Fe.
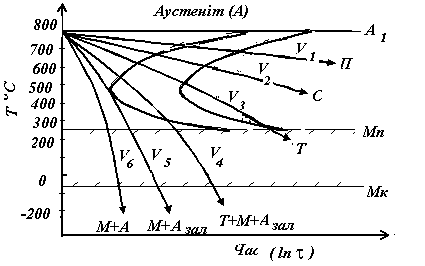
Рисунок 8.1 – Діаграма ізотермічного розпаду переохолодженого аустеніту з накладеними на неї кривими охолодження
Залежність критичної швидкості гартування від вмісту вуглецю в сталі подана на рис. 8.2. На vкр впливає також вид охолоджувального середовища, розмір зерна та легувальні елементи.
За зростанням інтенсивності охолодження охолодні середовища, що застосовують в практиці термічної обробки можна розташувати так: мінеральні мастила, вода, водяні розчини солей, кислот, лугів. Для гартування вуглецевих сталей краще вода або водяні розчини солей. Ідеальний охолодник при гартуванні той, що не викликає розпаду аустеніту на перлітні структури, забезпечуючи максимальну швидкість охолодження в інтервалі температур А1 – Мн і мінімально допустиму в мартенситному інтервалі, що виключає появу значних внутрішніх структурних і термічних напружень, жолоблення, тріщин. Недолік води як охолоджувача: висока швидкість охолодження в мартенситному інтервалі і різкий спад охолоджуючої спроможності при її нагріванні. Мінеральні мастила позбавлені цих вад, але характеризуються в декілька разів меншою охолодною спроможністю. Тому їх доцільніше застосовувати для охолодження легованих сталей, критична швидкість загартування яких менше, ніж вуглецевих.
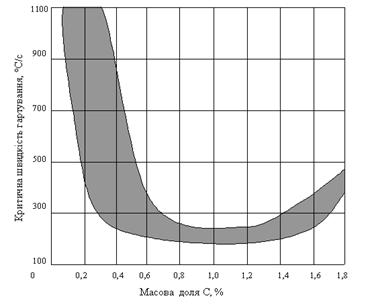
Рисунок 8.2 - Критична швидкість гартування залежно від вмісту вуглецю в сталі
При розрахунку тривалості нагрівання tн під термічну обробку можна керуватися табл. 8.1. Тривалість ізотермічної витримки (tв) беруть найчастіше рівною 1/5 від загальної тривалості нагрівання.
Таблиця 8.1 – Приблизна тривалість нагрівання стальних виробів
Тип нагрівального пристрою
|
Температура нагрівання, °С
|
Тривалість нагрівання (с) на 1 мм
діаметра виробу зі сталі
|
Полуменева піч
Електропіч
Соляна
ванна
|
800...900
770...820
820...880
770...820
820...8880
|
Вуглецевої
|
Легованої
|
60…70
60...65
50...55
12...14
10...12
|
65...80
70...75
60...65
18...20
16...18
|
Загартування доевтектоїдних сталей, що включає нагрівання до температур вище Ас3, тобто в аустенітний стан, називають повним. Для заевтектоїдних сталей використовують неповне гартування, при якому сталь, нагріта до температури дещо вищої за Ас1, набуває структури А+ЦІІ, при охолодженні проходить лише перетворення А ® М, тобто часткова (неповна) зміна структури. Зберігання деякої частки твердого і зносостійкого вторинного цементиту сприяє підвищенню механічних властивостей сталі. Повне загартування заевтектоїдних сталей із нагріванням до температур, що перевищують Асcm, призводить до підвищення вмісту в них аустеніту залишкового і погіршення властивостей загартованих сталей.
Неповне загартування доевтектоїдних сталей небажане, тому що після нього разом з твердим мартенситом зберігається м’який надлишковий ферит. В промисловості, залежно від характеру охолодження, застосовують різноманітні способи загартування: в одному охолоджувачі (неперервне гартування), у двох охолоджувачах (перервне гартування), ступінчасте, ізотермічне, гартування з самовідпуском. Завершальною операцією після гартування є відпуск сталі.
В і д п у с к (tempering, drawback) – операція термічної обробки, що полягає в нагріванні загартованої сталі до температур нижче Ас1, витримці при цій температурі, охолодженні. Мета відпуску – зменшення внутрішніх напружень у металі й одержання необхідних структури і властивостей.
Низький відпуск включає нагрівання загартованої сталі до 150 ... 250°С. Він застосовується для надання поверхневим шарам виробів високої твердості та зносостійкості. Низький відпуск, дещо зменшуючий внутрішні напруги, підвищує в’язкість сталі при зберіганні нею високої твердості, широко застосовують для виготовлення мірильного, різального і штампового інструменту (шаблони, фрези, мітчики, зубила, штампи, волоки та ін.), для деталей після насичення вуглецем ( після цементування). Структура сталі після низького відпуску називається мартенсит відпуску.
При середньому відпустку загартована сталь нагрівається до 300 ... 400 °С, чим забезпечується одержання структури трооститу відпуску, яка має достатню твердість (40...55 HRC) і міцність при високій межі текучості. Середній відпуск більшою мірою, ніж низький, сприяє зменшенню внутрішніх напружень і найбільш часто застосовується при термічній обробці ресор та пружин.
Високий відпуск включає нагрівання загартованої сталі до 500 ... 650°С і забезпечує отримання структури сорбіту відпуску з гарним комплексом властивостей (міцність, ударна в’язкість, твердість). Тому загартування з високим відпуском називають поліпшенням і застосовують для відповідальних деталей із середньовуглецевих сталей (колінчасті вали, шатуни тощо). При нагріванні загартованої сталі до температур вище 650 оС утворюється структура перліт відпуску.
На рис. 8.3 показано лівий кут діаграми стану Fe – Fe3C і температурні області нагрівання при термічній обробці сталей, а на рис. 8.4 - схему режимів різних видів термічної обробки.
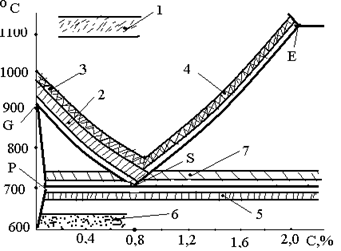
Рисунок 8.3 – Температурні області нагрівання при термічній обробці сталі 1 – дифузійний (гомогенізувальний) відпал; 2 – повний відпал, повне гартування; 3, 4 – нормалізація; 5 - рекристалізаційний відпал; 6 – відпуск; 7 – неповний відпал, неповне гартування
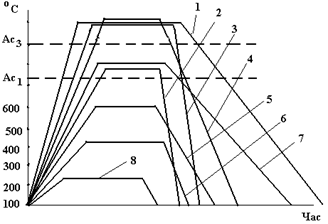
Рисунок 8.4 – Схеми режимів термічної обробки сталей: 1 – повний відпал; 2 – неповне гартування; 3 – повне гартування; 4 – нормалізація; 5 – високий відпуск; 6 – середній відпуск; 7 – неповний відпал; 8 – низький відпуск
На рис. 8.5 показана залежність механічних властивостей вуглецевої сталі від температури відпуску. За цією залежністю розрізняють низькотемпературний (низький), середньотемпературний (середній) і високотемпературний (високий) види відпуску.
Троостит, сорбіт і перліт відпуску на відміну від одержуваних з аустеніту при безперервному охолодженні мають зернисту, а не пластинчасту будову. Сталі з зернистою структурою характеризуються більш високою пластичністю і кращою оброблюваністю різанням.
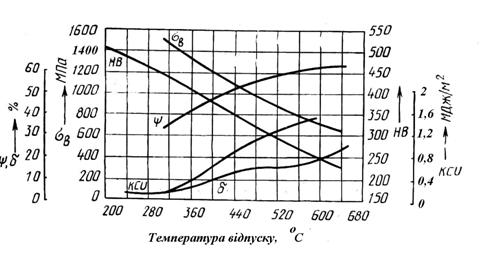
Рисунок 8.5 – Залежність механічних властивостей сталі від температури відпуску
Завдання на роботу
1. Призначити термічну обробку і скласти її режими для сталі відповідно до табл. 8.2.
2. Описати структуру після проведення призначеної термічної обробки.
3. Навести механічні властивості сталі після термічної обробки.
4. Зробити висновки і скласти звіт відповідно до завдання.
Таблиця 8.2 – Варіанти індивідуальних завдань
Варіант
|
Марка сталі
|
Мета термічної обробки
|
1
|
У12А
|
Зміцнювальна остаточна для інструмету
|
2
|
35
|
Виправлення структури після гарячої обробки тиском
|
3
|
10
|
Усунення ліквації в металургійних зливках
|
4
|
45
|
Пом’якшення сталі перед обробкою різанням
|
5
|
40Х
|
Остаточна зміцнювальна для зубчастих коліс
|
6
|
У10А
|
Пом’якшення сталі перед обробкою різанням
|
7
|
20
|
Пом’якшення сталі перед обробкою різанням
|
8
|
50
|
Усунення дефектів структури після гярячої ОМТ
|
9
|
25
|
Усунення дефектів структури після гярячої ОМТ
|
10
|
30
|
Покращення обробки різанням та як остаточна
|
11
|
50Л
|
Усунення дефектів структури
|
12
|
40
|
Остаточна зміцнювальна для валів
|
13
|
20
|
Усунення ліквації в металургійних зливках
|
14
|
60С2
|
Остаточна зміцнювальна
|
15
|
У13А
|
Ліквідація сітки вторинного цементиту
|
Контрольні питання для самопідготовки
1. Які лінії на діаграмі стану “залізо-вуглець” позначаються як А1, А2, А3, А4, Аcm ?
2. Які є види термічної обробки для сталей?
3. Які види відпалу сталей ви знаєте?
4. З якою метою призначають повний відпал доевтектоїдних сталей? До яких температур нагрівають ці сталі при повному відпалі?
5. З якою метою призначають неповний відпал доевтектоїдних сталей? До яких температур нагрівають ці сталі при повному відпалі?
6. З якою метою призначають відпал заевтектоїдних сталей? До яких температур нагрівають ці сталі при відпалі?
7. Яка термічна обробка називається нормалізацією? До яких температур нагрівають до- та заевтектоїдні сталі при нормалізації?
8. Які структури можуть утворюватися в сталях при їх різній швидкості охолодження з аустенітного стану?
9. В чому полягає термічна обробка “гартування” для сталей?
10. Яка швидкість охолодження сталей називається критичною?
11. Яка структура називається “мартенсит”?
12. Від чого залежить кількість залишкового аустеніту при гартуванні?
13. До яких температур нагрівають сталі різного хімічного складу при гартуванні?
14. Які види відпуску існують?
15. Для яких сталей призначають низький, середній та високий відпуск?
16. Яка термічна обробка сталей називається поліпшенням?

|