4.1 Контроль та управління процесами анаеробного бродіння
Для процесів анаеробного бродіння
виділяють три температурних режими, дотримання в межах яких є
необхідною умовою безперебійного вироблення біогазу і життєдіяльності
метаноутворювальних бактерій. Також до обмежувальних умов належить максимальна температура
нагрівального елемента, яка не може перевищувати 60°С. Нагрівання субстрату
відбувається за рахунок передачі тепла води, що протікає через нагрівальний
елемент. Вода гріється в котлі за рахунок спалювання виробленого біогазу.
При обертанні пластини активатора відбувається активне перемішування
субстрату, вирівнювання полів температур, інтенсифікація теплообміну між
нагрівником і субстратом. Для зменшення енерговитрат і збільшення виходу
біогазу необхідно контролювати і регулювати такі величини: температуру
поверхні нагрівального елемента; температуру субстрату в трьох шарах –
верхньому, середньому і нижньому; швидкість вібрування пластини-активатора
чи обертання мішалки. Для контролю і управління параметрами анаеробного
бродіння в біореакторі пропонується така схема управління (рис. 4.1) [37 -
39]. Управління за даною схемою можливе в реакторі з інтенсифікацією
теплообміну, запропонованому авторами (див. рис. 2.3). Температура субстрату
відслідковується сенсорамии
t2,
t3,
t4,
температура поверхні нагрівника − сенсором
t1.
За даними сенсора
t1
сервопривод триходового клапана на подачі
теплоносія на нагрівник регулює ступінь підмішування зворотного теплоносія.
За показами всіх
температурних сенсорів згідно із закладеною програмою в ЕОМ відбувається
управління двигуном – збурювачем
перемішувань субстрату за допомогою частотного регулятора. Кількість
обертів двигуна відслідковується тахометром. Для передачі інформації в ЕОМ
від датчиків і тахометра слугують пристрої спряження ПС1…ПС3. Для передачі
сигналів керування від ЕОМ до сервопривода і частотного регулятора слугують
пристрої спряження ПС4…ПС5.
Для інтенсифікації теплообміну вибрано спосіб вібрації середовища, що в
окремих випадках дозволяє збільшити тепловіддачу у десятки разів. Вібрація
чи перемішування середовища або нагрівального елемента приводить до
активного перемішування середовища, вирівнювання температури в об’ємі,
інтенсифікації теплообміну. Це в кінцевому випадку приводить до зменшення
площ теплообміну, покращення протікання технологічних процесів та
енергозбереження.

Рисунок 4.1 −
Схема автоматичного управління
параметрами реактора для анаеробного бродіння:
ЕОМ – контролер (мікрокомп’ютер),
БЖ – блок живлення,
t1,
t2,
t3,
t4
– сенсори температури, ПС1…ПС5 – пристрої спряження.
За показами всіх
температурних сенсорів згідно з закладеною програмою в стаціонарному
комп’ютері відбувається управління двигуном – збурювачем
перемішувань субстрату за допомогою частотного регулятора. Кількість
обертів двигуна відслідковується тахометром. Для передачі інформації в ЕОМ
від датчиків і тахометра слугують пристрої спряження ПС1…ПС3. Для передачі
сигналів керування від ЕОМ до сервопривода і частотного регулятора слугують
пристрої спряження ПС4-ПС5.
Від мікрокомп’ютера (контролера) оброблена
інформація направляється на стаціонарний комп’ютер, в якому за допомогою
спеціально розробленої програми вона подається у графічному вигляді і
записується у текстовий файл.
Принципову схему інформаційних зв’язків
експериментальної установки наведено на рис. 4.1.
Алгоритм програми
автоматичного моніторингу роботи БГУ реалізований на мові програмування
Object
Pascal
з використанням
IDE
Delphi 7. Робочі
вікна програми обробки та збору даних від експериментальної установки
наведено на рис. 4.2.
В головному вікні 1
(рис. 4.2) будуються графіки
залежності температур і кількості обертів вала двигуна від часу дослідження.
На інформаційній панелі 2 у відповідних комірках динамічно фіксуються дані
параметрів у вигляді числових значень.
Кнопки 3 – “R”
,“P”, “S”
відповідно: початок зчитування даних,
пауза і стоп – зупинення роботи. У вікнах 4 і 5 відбувається
налагодження роботи програми і роботи
COM
порта:
- інтервал таймера (1–20
сек, з інтервалом 0,1 сек);
- режим роботи програми
(безперервно, дискретно);
- мінімальні значення
відображення для всіх параметрів;
- максимальні значення
відображення для всіх параметрів.
Параметри настроювання
СОМ порту:
-
номер порту;
-
швидкість
передачі/прийому даних;
-
кількість біт
інформації;
-
тип контролю
достовірності інформації;
-
кількість стоп-біт.
Загальний вигляд
експериментального контролера наведено на рис. 4.3.
Структурно-логічні схеми
програми обробки та збору даних від експериментальної установки зображено на
рис. 4.4.
Всі пристрої спряження
конструктивно виконано у вигляді мікрокомп’ютера. Мікрокомп’ютер виконано на
базі однокристалічного мікроконтролера
PIC
16F876.
Програма дозволяє записувати дані з інтервалом в 1 секунду у текстовий
файл, який потім можна прочитати у табличному редакторі. Запис даних
ведеться у форматі: дата, час, кількість обертів валу двигуна, температура
першого датчика, температура другого датчика, температура третього датчика,
усереднена температура датчиків, що розміщені в нагрівальному елементі.
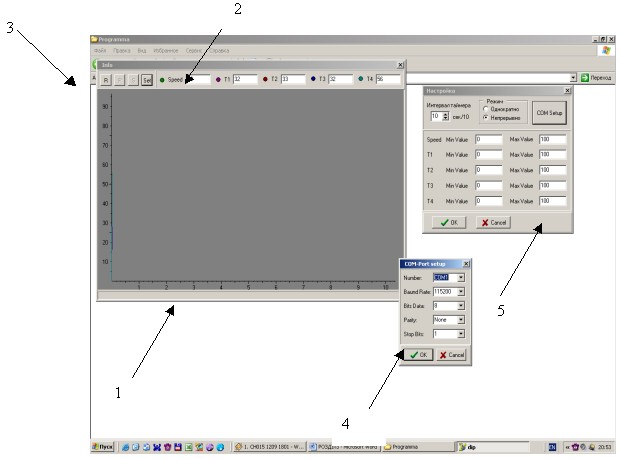
Рисунок 4.2 −
Робочі вікна програми оброблення та збору даних від експериментальної
установки
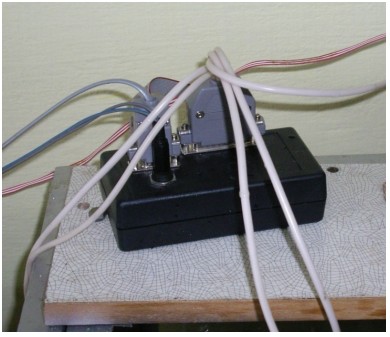
Рисунок 4.3
− Загальний вигляд експериментального
контролера
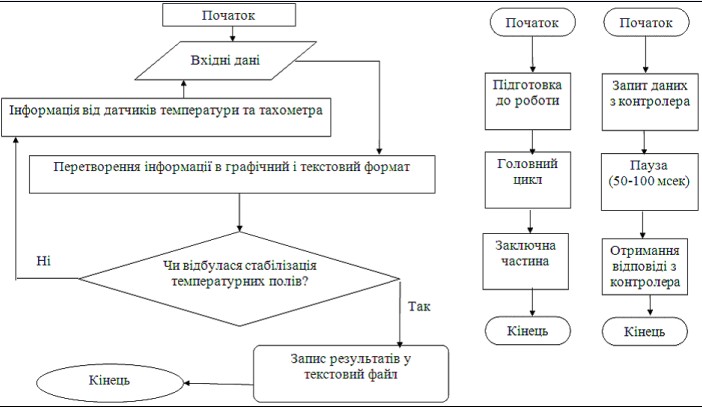
Рисунок 4.4 −
Структурно-логічні схеми
програми обробки та збору даних від БГУ
Загальний вигляд файла звіту проведеного
експерименту зображено на рис. 4.5
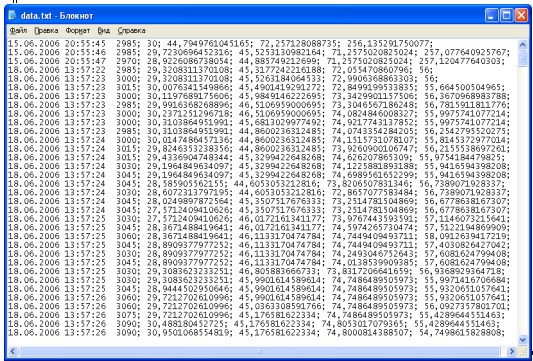
Рисунок 4.5 −
Загальний вигляд файла звіту роботи
системи термостабілізації та інтенсифікації БГУ
Згідно з [27] рівняння, що узагальнює відносний коефіцієнт тепловіддачі
через розмірні величини, апроксимується виразом

де
К – коефіцієнт інтенсифікації, що
є відношенням коефіцієнта тепловіддачі віброконвекції до
коефіцієнта тепловіддачі при вільній конвекції;
d
– діаметр циліндра
теплонагрівального елемента, мм;
ΔΤ – різниця між
температурою стінки нагрівника і середовищем С;
ΔА – амплітуда коливань
нагрівального елемента, мм;
f − частота коливань
нагрівального елемента, Гц.
В промисловості система
автоматизованого контролю за роботою БГУ виготовляється в вигляді шафи з
набором елементів для роботи установки: контролера, частотних
перетворювачів, автоматичних вимикачів тощо (рис. 4.6).
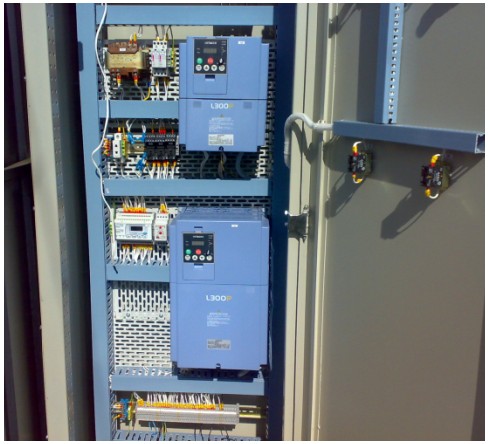
Рисунок 4.6 –
Шафа з пристроями автоматичного керування БГУ