Мета роботи - вивчення
фізичної суті дугового зварювання, технології, обладнання та
матеріалів для ручного дугового зварювання, виконання розрахунків
режиму зварювання, отримання практичних навичок виконання
найпростіших електрозварювальних робіт.
1 ЗАГАЛЬНІ ВІДОМОСТІ
Електричне дугове зварювання –
це процес з'єднання металевих заготовок шляхом розплавлення їх
кромок теплом електричної дуги з наступною сумісною кристалізацією
розплавленого металу.
1.1 Джерела зварювального
струму
Для дугового зварювання
застосовують як постійний, так і змінний струм. Джерелами
постійного струму служать зварювальні генератори постійного струму і
зварювальні випрямлячі.
При зварюванні змінним струмом
використовують переважно зварювальні трансформатори. Оскільки режим
дугового зварювання характеризується частими короткими замиканнями,
то для обмеження струму короткого замикання джерела струму у
більшості випадків мають так звану спадну зовнішню характеристику.
Зовнішньою характеристикою –
називається залежність між напругою U на затискувачах джерела струму
і струмом навантаження I. Спадною ж характеристикою називається
такий характер цієї залежності, коли зі збільшенням струму
навантаження напруга на клемах джерела струму зменшується.
На рис. 21 показано два види
зовнішніх характеристик: жорсткої 1 і спадної 2. Жорстку
характеристику звичайно мають джерела струму, які призначені для
силових або освітлювальних навантажень. Напруга у таких джерел при
зміні струму навантаження залишається постійною.
Якщо ж джерело струму має
спадну зовнішню характеристику, то зі збільшенням струму
навантаження напруга на затискачах джерела струму падатиме і це
приведе до обмеження струму короткого замикання.
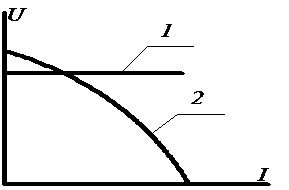 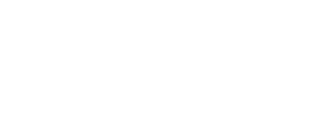
Спадну зовнішню характеристику
зварювального трансформатора отримуємо за рахунок того, що
послідовно з дугою і вторинною обмоткою трансформатора вмикають так
звану дросельну або реактивну обмотку. При проходженні зварного
струму у витках дросельної обмотки індукується е.р.с.
(електрорушійна сила) самоіндукції, яка має напрям, протилежний
основній е.р.с. трансформатора. Тому напруга, підведена до дуги,
знижується від значення холостого ходу (55 ... 80 В) до 15 ... 45
В під час горіння дуги і майже до нуля при короткому замиканні.
Є кілька схем вмикання
дросельної обмотки з трансформаторними обмотками (рис. 22). При
першій схемі (рис. 22, а) первинна І і вторинна II обмотки
знижувального однофазного трансформатора розташовані на залізному
сердечнику 1, а дросельна обмотка III - на сердечнику 2, які є
двома окремо виконаними апаратами.
При другій схемі вмикання
(рис. 22, б) трансформаторні (І - ІІ) і дросельна (ІІІ)
обмотки розташовані на спільному залізному сердечнику і являють
собою один апарат. Причому, та частина сердечника, на якій розміщені
обмотки І і II, є власне трансформатором, а частина, на якій
розташована обмотка ІІІ – дроселем. Сила зварювального струму
регулюється зміною повітряного зазору "С".
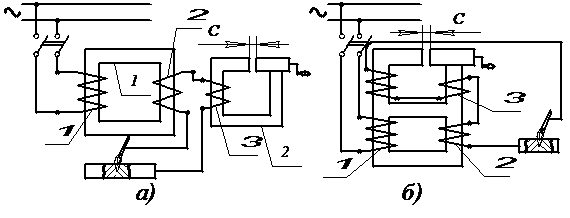
Рисунок 22 -
Схеми зварювальних трансформаторів:
І - первинна обмотка,
ІІ - вторинна обмотка, III - дросельна обмотка;
1
- сердечник трансформатора; 2 - сердечник дроселя
1.2 Електроди для ручного
дугового зварювання
Для ручного дугового зварювання
використовують електроди, що розплавляються, і електроди, що не
розплавляються. Найчастіше зварювання проводять електродами, що
розплавляються. Їх виготовляють із сталевого зварювального дроту у
вигляді стержнів діаметром від 1 до 12 мм (у більшості
випадків до 6 мм) і довжиною від 150 до 450 мм, на які
нанесені покриття. Електроди класифікують за такими ознаками:
матеріалом, з якого вони виготовлені; призначенням для зварювання
відповідних сталей; товщиною покриття, нанесеного на стержень; видом
покриття; характером шлаку, який утворюється при розплавленні
покриття; технічними властивостями металу шва; просторовими
положеннями зварювання, родом та полярністю зварювального струму.
Застосування електродів повинно
забезпечувати такі технологічні умови: легке запалювання і стійке
горіння дуги; рівномірне розплавлення покриття; рівномірне покриття
шва шлаком; легке відокремлення шлаку після зварювання; відсутність
непроварів, пор, тріщин та інших дефектів в металі шва.
Покриття на електроді виконує
такі функції:
- забезпечує стабільне горіння
дуги за рахунок зниження потенціалу іонізації повітряного простору
між електродом і деталлю, що зварюється. Для цього в покриття
вводяться крейда, мармур, силікати натрію і калію, поташ;
- забезпечує газовий захист
дуги, зони зварювання і розплавленого металу за рахунок речовин у
складі покриття, які легко розкладаються при високій температурі -
крохмалю, целюлози, магнезиту та ін.;
- забезпечує шлаковий захист
поверхні розплавленого металу. Шлакоутворюючими компонентами
покриття є марганцева руда, плавиковий шпат, рутил, мармур, крейда
та ін.;
- розкислення металу
зварювальної ванни. Як розкислювачі застосовують феромарганець,
феросиліцій;
- легування металу шва
феросплавами. Як скріплювач перерахованих компонентів звичайно
використовують рідке скло (силікат натрію Nа2O (SiO2)m).
2 ТЕХНОЛОГІЯ РУЧНОГО ДУГОВОГО
ЗВАРЮВАННЯ
2.1 Підготовка металу до
зварювання
Підготовка металу до зварювання
складається з правки, очистки, розмітки і збирання підготовлених
деталей для зварювання. Правкою ліквідують деформацію прокатаної
сталі, з якої головним чином і виготовляють зварні конструкції.
Очищення кромок від іржі, забруднень проводять металевою щіткою,
роблять це, а також сушку вологих місць, досить ретельно, щоб
запобігти утворенню в зварних швах пор, раковин, різних включень та
інших дефектів. Різку при підготовці деталей застосовують головним
чином термічну (вогневу). Механічне різання доцільно виконувати при
заготовці однотипних деталей, підготовці кромок. Зібрані вузли і
деталі з'єднують прихватками, які являють собою короткі шви з
поперечним перерізом 1/3 поперечного перерізу повного шва. Довжина
прихватки 20 ... 100 мм залежно від товщини листів і
довжини шва.
2.2 Підготовка кромок під
зварювання
При зварюванні у стик листів
товщиною до 6 мм кромки не скошують (рис. 23, а). Для
досягнення необхідного провару листи розташовують з зазором 2 ... 4
мм. При товщині листів від 6 до 20 мм роблять \/ -
подібний скіс кромок під кутом 60 ... 70о (рис. 23, б).
Біля вершини кута залишають притуплення 3 ... 5 мм щоб
запобігти пропалу і для зменшення кількості наплавленого металу. Між
листами залишають зазор 2 ... 4 мм для покращання провару
вершини шва. Для стикових швів в горизонтальному положенні звичайно
роблять скіс кромки одного листа під кутом 45° (рис. 23,
в). При зварюванні листів товщиною більше 20 мм
роблять X- або К-подібну розробку (рис. 23, г, д). Для
зварювання у стик більших товщин роблять чашоподібну підготовку
кромок (рис. 23, е).
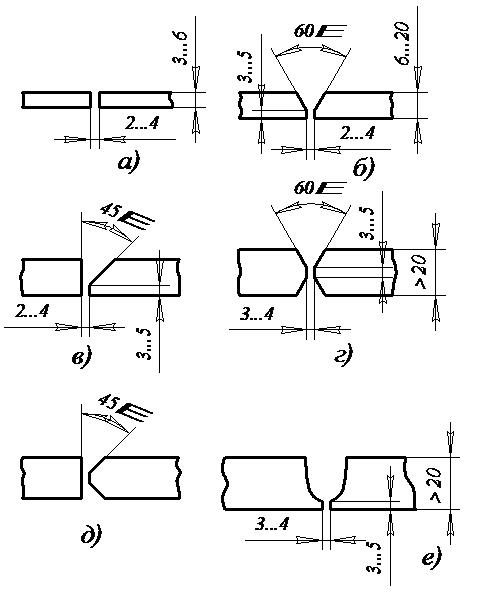
Рисунок 23 - Підготовка
кромок для ручного дугового зварювання у стик
При зварюванні кутовими швами
з'єднань внапусток (рис. 24, а) кромки не скошують, а тільки
очищають від окалини, іржі та забруднень. Таврові з'єднання часто
зварюють без скосу кромок (рис. 24, б). В конструкціях
таврових з'єднань, що працюють при динамічних навантаженнях,
рекомендується робити підготовку кромок стінки з V- або К-подібною
розробкою (рис. 24, в,
г).
У всіх випадках кромки листів,
що підлягають зварюванню, повинні бути очищені від іржі, окалини та
інших забруднень. Підготовка кромок під зварювання виконується на
стругальному або фрезерному верстаті, а також за допомогою газорізки
з наступною очисткою від окалини.
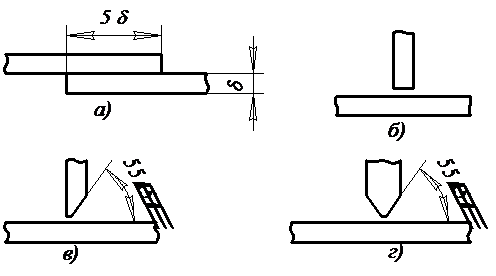
Рисунок 24 - Підготовка кромок
для кутових швів:
з'єднань внапусток (а) і
таврових (б - г)
2.3 Вибір режиму зварювання
Під режимом зварювання
розуміють сукупність показників, які визначають характер протікання
процесу зварювання. Ці показники впливають на кількість тепла, що
вводиться у виріб при зварюванні. До основних показників режиму
зварювання відносяться: діаметр електрода, сила зварювального
струму, напруга на дузі і швидкість зварювання. Допоміжними
показниками режиму зварювання вважаються вид і полярність струму,
тип і марка покриття електрода, кут нахилу електрода, температура
попереднього нагріву металу.
Вибір режиму ручного дугового
зварювання часто обмежується визначенням діаметра електрода і сили
зварювального струму. Швидкість зварювання і напруга на дузі
встановлюються зварником залежно від виду зварного з'єднання, марки
сталі, марки електрода, положення шва у просторі.
Діаметр електрода вибирається
залежно від товщини зварюваного металу, виду зварного з'єднання,
типу шва тощо. При стиковому зварюванні листів товщиною до 4 мм
у нижньому положенні діаметр електрода береться рівним товщині
листа. При зварюванні сталі більшої товщини беруть електроди
діаметром 4 ... 6 мм за умови забезпечення повної можливості
проварювання металу деталей, що з'єднуються, і правильного
формування шва.
В багатошарових стикових і
кутових швах перший шар чи прохід виконується електродом діаметром 2
... 4 мм, наступні шари і проходи виконуються електродами
більшого діаметра.
Зварювання у вертикальному
положенні звичайно виконується електродами діаметром не більше 4
мм, електроди більшого (5 ... 6 мм) діаметра можуть
застосовуватись тільки зварниками високої кваліфікації.
Стельові шви звичайно
виконуються електродами діаметром не більше 4 мм.
Силу зварювального струму
вибирають залежно від діаметра електродів за формулою
І = К
×
d , А,
де К - коефіцієнт,
що дорівнює 35 .. .60 А/мм,
d
- діаметр електрода, мм.
Відносно малий cтрум призводить
до нестійкого горіння дуги, непровару і низької продуктивності.
Надто великий – до сильного перегріву електрода при зварюванні,
збільшення швидкості розплавлення електрода, підвищеного
розбризкування електродного матеріалу і погіршення формування шва.
При зварюванні вертикальних і
горизонтальних швів струм повинен бути меншим за прийнятий для
зварювання у нижньому положенні приблизно на 5 ... 10%, а для
стельових на 10 ... 15% для того, щоб рідкий метал не витікав із
зварювальної ванни. Положення швів у просторі показане на рис. 25.
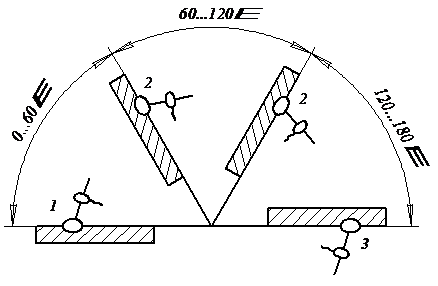
Рисунок 25 –
Положення зварних швів у просторі:
1
– нижнє; 2 – вертикальне або горизонтальне; 3 –
стельове
2.4 Техніка
виконання швів
Запалювання
дуги. Існує два способи запалювання дуги електродами з
покриттям - прямим відривом електрода і відривом по кривій. Перший
спосіб називається запалюванням впритул; другий - нагадує рух при
запалюванні сірника і його називають чирканням.
Довжина дуги.
Одразу після запалювання дуги починається плавлення металу. Довжина
дуги повинна бути постійною. Від правильно вибраної довжини дуги
значною мірою залежить продуктивність зварювання і якість зварного
шва.
Нормальною вважається
довжина дуги, що дорівнює 0,5 ... 1,1 діаметра електрода стержня.
Збільшення довжини дуги знижує стійкість її горіння, глибину
проплавлення основного металу, збільшує витрати на угар і
розбризкування металу, викликає утворення шва з нерівною поверхнею і
збільшує вплив навколишньої атмосфери на розплавлений метал.
Швидкість подачі
електрода в дугу повинна дорівнювати швидкості розплавлення
електрода.
Положення електрода.
Нахил електрода при зварюванні залежить від положення зварювання у
просторі, товщини і складу зварюваного металу, діаметра електрода,
виду і товщини покриття. Напрям зварювання може бути зліва направо,
справа наліво, від себе і на себе (рис. 26, а). Незалежно
від напряму зварювання положення електрода повинно бути певним: він
повинен бути нахиленим до осі шва так, щоб метал виробу проплавлявся
на найбільшу глибину. Для отримання щільного і рівного шва при
зварюванні у нижньому положенні на горизонтальній площині кут нахилу
електрода повинен бути 15° від вертикалі у бік ведення шва
(рис. 26, б).
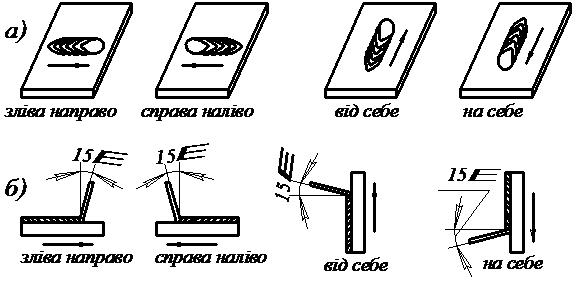
Рисунок 26 - Напрям зварювання
(а) і нахил електрода (б)
Кут нахилу електрода при
ручному дуговому зварюванні у різних просторових положеннях шва
наводиться на рис. 26, б.
Коливальні рухи електрода.
Для отримання валика потрібної ширини проводяться поперечні
коливальні рухи електрода. Якщо пересувати електрод тільки вздовж
осі шва без його поперечного коливання, то ширина валика
визначається тільки силою зварювального струму і швидкістю
зварювання і складає 0,8 ... 1,5 діаметра електрода. Такі вузькі
(ниткові) валики застосовують при зварюванні тонких листів, при
накладанні першого кореневого шару багатошарового шва та в деяких
інших випадках.
Найчастіше використовують шви
шириною від 1,5 до 4 діаметрів електрода, які одержують за допомогою
поперечних коливальних рухів.
Найбільш поширені види
поперечних коливальних рухів електрода при ручному зварюванні (рис.
27): прямі по ламаній лінії; півмісяцем, поверненим кінцями до
наплавленого шва; півмісяцем, поверненим кінцями до напряму
зварювання; трикутниками; петлеподібні з затримкою у певних місцях.

Рисунок 27 - Основні
види поперечних рухів кінця електрода:
а - г
при звичайних швах;
д - ж
- при швах з посиленим прогріванням кромок
Поперечні коливання по ламаній
лінії часто застосовують для одержання наплавних валиків, при
стиковому зварюванні листів без скосу кромок в нижньому положенні і
в тих випадках, коли немає небезпеки пропалювання зварюваної деталі.
Рухи півмісяцем застосовують
для стикових швів зі скосом кромок і для кутових швів з катетом
менше 6 мм, які виконуються у будь-якому положенні електродом
діаметром до 4 мм.
Рухи трикутником застосовують
при виконанні кутових швів з катетом шва більше 6 мм і
стикових із скосом кромок у будь-якому просторовому положенні.
Петлеподібні рухи застосовують у випадках, які потребують більшого
прогріву металу по краях шва, головним чином, при зварюванні листів
із високолегованих сталей. Ці сталі мають високу текучість і для
задовільного формування шва потрібно затримувати електрод на краях,
щоб попередити пропалювання в центрі шва і витікання металу із
зварної ванни при вертикальному зварюванні.
Способи заповнення шва по
перерізу. За способом заповнення шва по
перерізу розрізняють одношарові шви (рис. 28, а),
багатопрохідні багатошарові (рис. 28, б) і багатошарові (рис.
28, г).
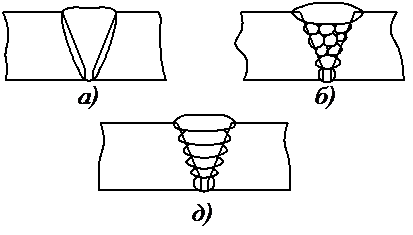
Рисунок 28 -
Схеми заповнення швів по перерізу:
а)
- одношаровий і однопрохідний;
б)
- багатошаровий і багатопрохідний;
в)
- багатошаровий
Якщо число шарів дорівнює числу
проходів, то такий шов називається багатошаровим. Якщо деякі з шарів
виконують за кілька проходів, то такий шов називають
багатопрохідним.
Багатошарові шви найчастіше
використовують у стикових з'єднаннях, багатопрохідні - в кутових і
таврових.
3 ВИДИ І ПРИЧИНИ БРАКУ
Дефектами зварних швів
називають різні відхилення від встановлених норм і технічних вимог,
що висуваються до зварних з'єднань. Дефекти зменшують міцність
зварних з'єднань і можуть призвести до руйнування всієї конструкції.
До дефектів форми шва
відносять: нерівномірні ширину і висоту шва, хвилястість шва,
неоднакові розміри катетів кутових швів. Причиною їх утворення є
коливання напруги, нерівномірність швидкості зварювання, недостатня
кваліфікація зварника.
Напливи
(рис . 29, а) утворюються в результаті
натікання рідкого металу на кромки холодного основного металу. Це
відбувається внаслідок надмірного струму, неправильного нахилу
електрода.
Підрізи
(рис. 29, б) являють собою продовгуваті заглибини (канавки),
які утворились в основному металі по кореню шва внаслідок надмірного
струму і напруги на дузі.
Незаплавлені кратери
утворюються при різкому обриванні дуги. Вони зменшують переріз шва і
можуть бути місцем утворення тріщин. Пропалюванням називають
проплавлення основного металу і утворення наскрізних отворів. Вони
утворюються внаслідок великого зазору, надмірного струму при високих
швидкостях зварювання.
Газові пори
утворюються внаслідок перенасичення рідкого металу газами, які не
встигли вийти на поверхню в процесі швидкого затвердіння шва.
Причиною пор є:
- іржа, масло і фарба на
кромках основного металу і на поверхні електродів;
- використання вологих
електродів;
- надмірна швидкість
зварювання, що призводить до порушення газового захисту ванни
рідкого металу;
- неправильно вибрана марка
електродів.
Шлакові включення
(рис. 29, в) утворюються внаслідок незадовільної зачистки
кромок металу і електродів від окалини, іржі та інших забруднень.
Непровари
(рис. 29, г) - це несплавлення основного металу з
наплавленим, їх основна причина - недостатня сила струму і
відхилення електрода від осі шва.
Тріщини
(рис. 29, д) є найбільш небезпечним дефектом зварних швів.
Вони можуть виникати як у самому шві, так і в навколошовній зоні.
Однією з багатьох причин утворення тріщин є підвищений вміст
вуглецю, який сприяє утворенню структур загартування. На утворення
тріщин впливає також підвищений вміст у наплавленому металі
шкідливих елементів - сірки та фосфору.
4 СПОСОБИ КОНТРОЛЮ ЯКОСТІ
ЗВАРНИХ ШВІВ І З'ЄДНАНЬ
Якість зварювання визначає
надійність і довговічність зварних конструкцій. Сучасна зварювальна
техніка має у своєму розпорядженні різноманітні методи контролю
якості зварювання.
Зовнішній огляд і обміри
зварних швів. Цьому способу контролю
піддають заготовки деталей і готові зварні шви. Мета зовнішнього
огляду заготовок - виявити вмיּятини, задирки та інші дефекти а також
бруд, масло, іржу, окалину на поверхні кромок.
Мета зовнішнього огляду готових
зварних з'єднань - виявити зовнішні дефекти (непровари кореня
стикового шва, напливи, підрізи, незаварені кратери, зовнішні
тріщини тощо).
Зовнішньому огляду піддають усі
шви, незалежно від того, який спосіб контролю буде застосовано в
подальшому.
Контроль непроникності швів.
Цей спосіб полягає у контролі за проникненням газів (повітря, суміші
повітря з аміаком і іншими індикаторами) та рідин (води, гасу) через
щонайменші дефекти несуцільності. Він широко застосовується для
перевірки герметичності посудин і трубопроводів.
Гідравлічні випробування.
Ними контролюється не тільки щільність зварних з'єднань, але і
відносна міцність всієї зварної конструкції. При гідравлічних
випробуваннях посудина наповнюється водою, потім в ній гідравлічним
пресом створюється тиск, що дорівнює робочому. Якщо дефектів не
виявлено, то тиск підвищується до Р = (1,25 ... 1,50)·Рроб.
Пневматичні випробування
виконують з метою контролю щільності зварних з'єднань в посудинах,
які працюють під тиском.
Рентгенівське просвічування
основане на властивості рентгенівських променів проникати через
непрозорі тіла, ослаблювати свою інтенсивність залежно від пустот,
включень і тріщин. При наявності дефектів у швах, рентгенівські
промені ослаблюються неоднаково і на проявленій фотоплівці
з'являються місця з різною інтенсивністю затемнення, за якими і
роблять висновок про характер і розміри дефектів.
Рентгенівське просвічування
дозволяє виявити такі внутрішні дефекти як тріщини, непровари,
шлакові включення, газові пори.
Магнітографічний метод
контролю. Суть цього методу полягає у
намагнічуванні зварних швів і фіксації магнітного потоку на
феромагнітну стрічку.
Ультразвуковий контроль
зварних швів полягає у здатності ультразвукових хвиль проникати в
метал на велику глибину і відбиватися від неметалевих включень,
пустот, тріщин тощо.
Металографічні випробування
зварних швів дозволяють на зразках, вирізаних із шва, виявити
структуру металу і її відповідність заданій.
Механічні випробування
виконують на зразках, вирізаних із зварного з'єднання або зварених
окремо. Це випробування на міцність, твердість, згин, ударну
в'язкість та інші.
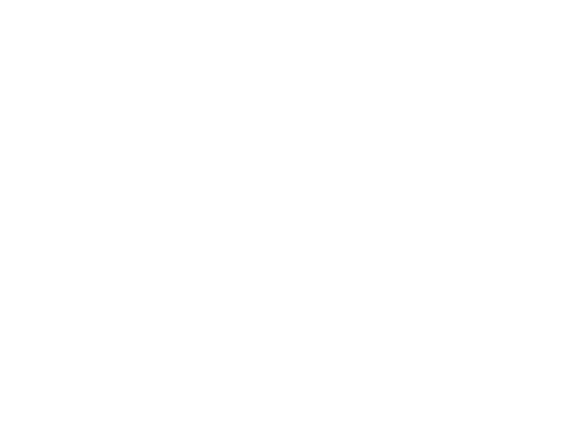
Рисунок 29 - Дефекти
зварних з'єднань
5 ПОРЯДОК ВИКОНАННЯ РОБОТИ
1.
Ознайомитись та засвоїти правила техніки
безпеки при роботі зі зварювальним устаткуванням.
2.
Підготувати до зварювання зразки:
очистити від іржі, масла та іншого бруду, підготувати кромки і
скласти зразки під зварювання.
3.
Вибрати тип і діаметр електродів.
4.
Призначити режим зварювання.
5.
Включити живлення, запалити дугу,
виконати зварювання.
6.
Провести
контроль якості шва зовнішнім оглядом.
7.
Скласти звіт про
роботу.
6 ЗМІСТ ЗВІТУ
Звіт про роботу повинен
вміщувати:
1.
Короткі
теоретичні відомості про зварювання плавленням;
2.
Короткі
теоретичні відомості про зварювальне обладнання;
3.
Відомості про
електроди;
4.
Відомості про
типи зварних з'єднань;
5.
Відомості про
техніку виконання зварних швів;
6. Завдання
на самостійну роботу: матеріал зразків,тип з'єднання, тип та діаметр
електрода, розрахунки режиму зварювання, результати контролю шва;
7. Результати
дослідів занести у таблицю 8.
Таблиця 8 –
Результати дослідів
Марка
матеріалу |
Товщина
зразків,
мм |
Тип з'єд-нання |
Діаметр
електрода, мм |
Сила струму,А |
Контроль шва |
Дефект шва |
Причина
дефекту |
|
|
|
|
|
|
|
КОНТРОЛЬНІ ПИТАННЯ ДЛЯ
САМОПІДГОТОВКИ
1.
Суть та схеми ручного дугового
зварювання.
2.
Класифікація електродів для ручного
дугового зварювання.
3.
Основні параметри режиму при ручному
дуговому зварюванні.
4.
Розрахунок режимів зварювання.
5.
Технологія
ручного дугового зварювання.
6.
Що називається зварювальною дугою?
7.
Класифікація електродів для ручного
дугового зварювання.
8.
Призначення та види покриттів
електродів.
9.
Основні величини, які характеризують
процес зварювання.
10.
Як змінюється коефіцієнт втрат на угар
та розбризкування електрода із зміною довжини дуги?
11.
Що викликає появу пор у металі шва?
12.
Підготовка крайок під зварювання.
|