Мета роботи: вивчити типові способи обробки отворів,
інструмент, що при цьому застосовується, основні типи свердлильних
верстатів; навчитися вибирати режими різання процесів обробки
отворів; набути навичок роботи на вертикально-свердлильних
верстатах.
1 ТЕОРЕТИЧНІ ВІДОМОСТІ
Обробка заготовок на
свердлильних верстатах - розповсюджений метод отримання отворів з
різною точністю розмірів і шорсткістю поверхні. Процес різання
здійснюється за рахунок обертального руху інструмента або заготовки
(головного руху) і одночасного переміщення інструмента вздовж осі
(руху подачі).
На свердлильних верстатах
отримують отвори як в суцільному матеріалі, так і збільшують діаметр
готових отворів (литих, штампованих, попередньо просвердлених).
На свердлильних верстатах
виконують такі основні технологічні процеси:
свердління глухих і наскрізних
отворів у суцільному матеріалі за допомогою свердел як по розмітці,
так і по кондукторах (рис. 40, а). Свердління як закінчена
операція виконується тоді, коли точність отвору не перевищує 12
квалітету, а шорсткість – 3 ... 4 класів;
розсвердлювання (рис. 40,
б) - процес збільшення свердлом діаметра наявних отворів,
головним чином просвердлених. Отвори, одержані литтям, штампуванням,
розсвердлювати не рекомендується через сильне відхилення свердла
внаслідок неправильної форми отворів або незбігу центра отвору з
віссю свердла;
зенкерування (рис. 40, в)
- процес обробки циліндричних литих, штампованих або попередньо
просвердлених отворів зенкером для надання їм правильної
геометричної форми, потрібних розмірів і необхідної шорсткості
поверхні;
розточування отворів (рис. 40,
г, д) – здійснюється різцями у тих випадках, коли осі їх
повинні бути розташовані за точними координатами;
розвертання (рис. 40, е, ж)
– процес остаточної обробки отворів розвертками з метою надання їм
точних розмірів і високої чистоти поверхні;
зенкування (рис. 40, и, к)
– процес одержання циліндричних або конічних заглиблень у попередньо
просвердлених отворах під головки болтів, гвинтів і інших деталей за
допомогою циліндричних і конічних зенкерів (зенківок);
цекування – обробка торцевих
поверхонь під гайки, шайби, кільця пластинками або торцевими
зенкерами (рис. 40, л, м);
нарізання різьби в отворах
може здійснюватися на свердлильних верстатах гайкорізами (рис. 40,
н).
При нарізанні різьби в глухих
отворах верстат повинен мати пристрій для реверсивного (зворотного)
обертання шпинделя для викручування гайкоріза з нарізаного отвору. З
цією метою застосовують також спеціальні патрони, що дають змогу
змінювати напрям обертання гайкоріза без зміни напряму обертання
шпинделя верстата.
Найбільш поширеною схемою
обробки отворів свердлами, зенкерами, розвертками є така, коли
головний рух надається інструменту. Однак при цьому вісь отвору може
відхилятися вбік. Це відхилення зростає із збільшенням глибини
отвору. Тому при свердлінні глибоких отворів, у яких глибина
перевищує діаметр у 5 і більше разів, обертального руху надають
заготовці, а поступального – свердлу. При цьому відхилення осі
отвору вбік значно зменшується.
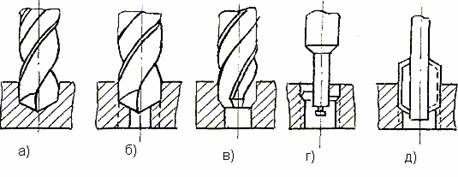
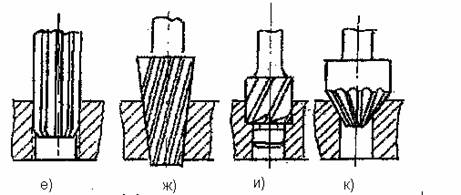
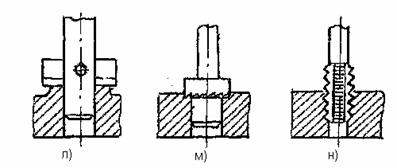
Рисунок 40 –
Схеми одержання і обробки отворів
на свердлильних верстатах
1.2 Різальний інструмент
1.2.1 Свердла
Свердла виготовляють діаметром
від 0,1 до 200 мм. Розрізняють такі основні типи свердел:
перові (рис. 41, а), що
являють собою стержень або закріплювану в оправці пластинку з
різальними кромками, заточеними під кутом 2
j
= 80 ... 150°. Застосовують їх рідко, в основному для свердління
отворів у твердих поковках і виливках та для обробки ступінчастих
отворів;
спіральні
(рис. 41, б),
які широко застосовують при роботі на свердлильних та інших
верстатах для отримання отворів. Величина кута між головними
різальними кромками, утвореними перетином передніх і задніх
поверхонь, при обробці сталі і чавуну береться 2j
= 118°, для свердління м'яких і в'язких матеріалів (алюмінію,
магнію) 2j
= 80 ... 90°, для свердління твердих і крихких матеріалів – 2j
= 130 ...
140°.
Для свердління отворів у
твердому чавуні, загартованій сталі і інших матеріалах підвищеної
твердості великого поширення набули спіральні свердла, оснащені
пластинками з твердих сплавів, що дає змогу значно підвищувати
режими різання і продуктивність праці.
свердла для глибокого
свердління (рис. 41, в), що використовуються при свердлінні
отворів діаметром до 80 мм, глибина яких перевищує діаметр в
5 і більше разів;
центрувальні (рис. 41, г),
які служать для одержання центрових отворів у деталях машин, що
обробляються в центрах на токарних верстатах;
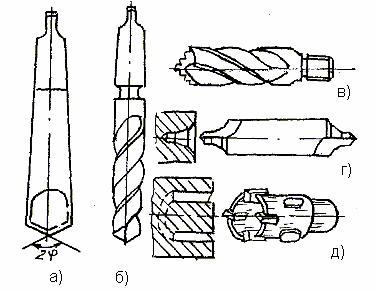
Рисунок 41
–
Свердла
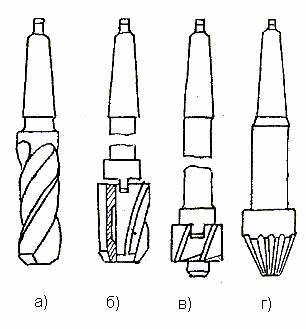
Рисунок 42 – Типи
зенкерів
свердла для кільцевого
свердління (рис. 41,
д), що застосовуються при свердлінні глибоких отворів
діаметром від 90 до 200 мм. При кільцевому свердлінні в
стружку відходить тільки вузька кільцева частина матеріалу, а
серцевина залишається суцільною і може бути використана.
1.2.2 Зенкери
Залежно від призначення
розрізняють такі основні типи зенкерів:
а) спіральні (рис. 42, а, б),
що застосовують для обробки наскрізних отворів;
б) циліндричні - з напрямною
цапфою (рис. 42, в), які служать для обробки торцевих площин
або отворів під циліндричні головки гвинтів;
в) конічні (зенківки)
(рис. 42, г) що
застосовують для зенкування конічних заглиблень у циліндричних
отворах.
За способами кріплення
розрізняють зенкери хвостові
(рис. 42, а) і насадні (рис. 42, б).
Зенкери виготовляють
суцільними, з напаяними пластинками і збірними з вставними ножами.
Наявність більшої кількості
зубців у порівнянні з свердлом підвищує стійкість і продуктивність
зенкерів, а також точність отворів і чистоту їх поверхні.
Зенкерування отворів більш
продуктивна операція, ніж розсвердлювання, оскільки може
здійснюватися з подачами в 2 ... 2,5 раза більшими, ніж свердління;
воно забезпечує одержання отворів 9 ... 11 квалітетів і 4 ...
5 класів шорсткості поверхні.
1.2.3 Розвертки
Залежно від способу
застосування розвертки поділяються на ручні і машинні.
За конструктивними
особливостями розвертки поділяються на хвостові і насадні, суцільні
і з вставними ножами.
За формою оброблюваного отвору
розрізняють розвертки циліндричні, конічні і ступінчасті.
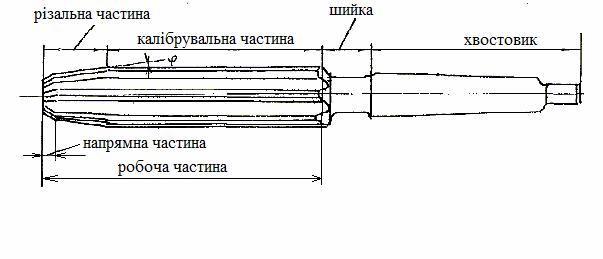
Рисунок 43 – Розвертка
Розвертка складається з робочої
частини, шийки і хвостовика (рис. 43). До робочої частини
входять ріжуча і калібрувальна частини. Різальна частина виконує
основну роботу різання. Кут
j
для ручних розверток беруть таким, що дорівнює 1... 2°, а у машинних
для обробки крихких і твердих матеріалів
j
= 3 ... 5° і для в'язких матеріалів – 12 ... 15°.
Калібрувальна частина спрямовує
розвертку в отворі, надає йому потрібної точності і шорсткості
поверхні.
Число зубців розверток від 6 до
12 і більше. За допомогою розверток одержують отвори 7 ... 11
квалітетів і 7 ... 9 класів шорсткості.
1.3 Режими різання
При свердлінні глибина
різання дорівнює половині діаметра отвору
D:
t
= D/2,
мм,
При розсвердлюванні,
розвертанні і зенкеруванні глибина різання
t
= (D
– d)/2,
мм,
де
D -
діаметр отвору після обробки, мм;
d -
діаметр отвору до обробки, мм.
Величину подачі при свердлінні
визначають за емпіричною формулою
S
=
CD0,6,
мм/об,
де С - коефіцієнт, який
залежить від матеріалу, що обробляється, точності і шорсткості
поверхні отвору. Значення С беруть з довідників.
При зенкеруванні величина
подачі береться приблизно в 2 ... 2,5 раза більша, ніж при
свердлінні. Залежно від оброблюваного матеріалу, діаметра зенкера і
точності отвору вона змінюється в межах від 0,2 до 3,4 мм/об.
При розвертанні величина подачі
може змінюватися від 0,2 до 7,5 мм/об.
При чистовому розвертанні точних отворів подача не повинна
перевищувати 1 ... 1,5 мм/об.
Швидкість різання при обробці
отворів
V =
pDn
/ 1000, м/хв,
де
D - діаметр різального
інструменту, мм;
n - число його обертів
за хвилину.
1.4 Свердлильні верстати
Свердлильні верстати
поділяються на такі основні типи:
1. Вертикально-свердлильні -
найбільш поширені верстати, що застосовуються в одиничному і
серійному виробництві. Основною характеристикою їх є найбільший
діаметр отвору, який можна свердлити на них в сталі середньої
твердості. Цей діаметр в сучасних вертикально-свердлильних верстатах
складає 6, 12, 18, 25, 35, 50 і 75 мм.
Загальний вигляд
вертикально-свердлильного верстата показано на рис. 44. Він
складається з фундаментної плити 7, станини 6, коробки швидкостей 4,
шпинделя 2, коробки подач 3 і стола 1, на якому встановлюється
оброблювана деталь. Для закріплення деталей на столі верстата
застосовують універсальні і спеціальні пристрої. До універсальних
затискних пристроїв відносяться притискні планки, призми, машинні
лещата, кутники. Для забезпечення правильного положення інструмента
відносно осі оброблюваного отвору і спрямування його під час роботи
застосовують спеціальні пристрої – кондуктори.
2.
Радіально-свердлильні верстати призначені для обробки отворів у
великих і важких деталях. Загальний вигляд такого верстата показано
на рис. 45. Навколо нерухомої колони 2, закріпленої на фундаментній
плиті 1, може повертатися на кут 360° гільза 3, по якій за допомогою
електродвигуна 5, зубчастої передачі і гвинта 6 може переміщуватися
вверх і вниз та закріплюватися у потрібному положенні траверса 4. По
напрямних траверси вручну переміщується шпиндельна головка 8,
всередині якої вміщена коробка швидкостей і коробка подач, за
допомогою яких шпиндель 9 дістає обертання і осьову подачу. В
конічному отворі шпинделя закріплюється різальний інструмент.
Оброблюваний виріб встановлюється на плиті 1 або на столі 10.
В результаті переміщення
шпиндельної головки по траверсі і обертання траверси вісь шпинделя
можна встановити в будь-якій точці площини, обмеженої колами,
радіуси яких дорівнюють найбільшій і найменшій відстані осі шпинделя
від осі колони 2. Таким чином, при обробці отворів у великих і
важких деталях при переході від одного отвору до другого не треба
пересувати деталь, а у відповідне місце переміщується шпиндель
верстата.
3. Багатошпиндельні свердлильні
- мають кілька шпинделів, взаємне розташування яких може бути
постійним або змінюватися залежно від оброблюваної деталі. Ці
верстати широко застосовуються в серійному і
масовому виробництві.
4. Горизонтально-свердлильні –
застосовуються для свердлення глибоких отворів. В цих верстатах
обертається оброблювана деталь, а свердло має лише поздовжню подачу.
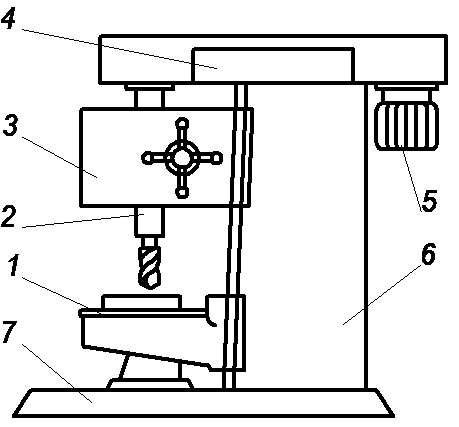
Рисунок 44 –
Загальний вигляд вертикально-свердлильного верстата
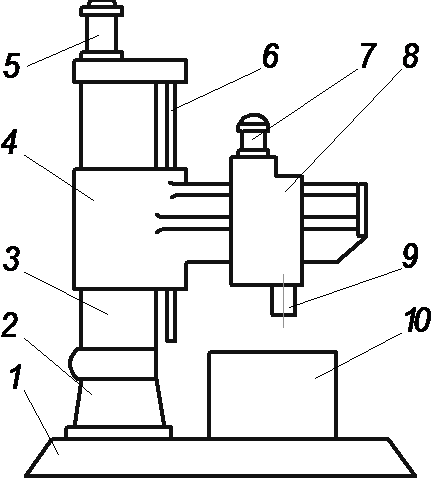
Рисунок 45 –
Загальний вигляд радіально–свердлильного верстата
2 ПОРЯДОК ВИКОНАННЯ РОБОТИ
1.
Вивчити методи, інструмент та технологію
обробки отворів на свердлильних верстатах.
2.
Ознайомитись з конструкцією, принципом
роботи, призначенням рукояток управління вертикально-свердлильного
верстата.
3.
Виконати розрахунки режиму різання при
свердлінні, зенкеруванні та розвертанні за заданими викладачем
вхідними даними.
4.
Виконати обробку отворів свердленням,
зенкеруванням, розвертанням.
5.
Скласти звіт про роботу.
3 ЗМІСТ ЗВІТУ
Звіт про виконану роботу
повинен вміщувати:
1.
Короткі теоретичні відомості про обробку
отворів на свердлильних верстатах;
2.
Схеми обробки поверхонь на свердлильних
верстатах;
3.
Ескізи різального інструменту
для обробки отворів (свердел, зенкерів, розверток);
4.
Ескіз загального вигляду
вертикально-свердлильного верстата;
5.
Розрахунки режимів різання за вказаними
даними;
6.
Описання ходу та результатів виконаної
роботи із обробки отворів;
7.
Висновки.
4 КОНТРОЛЬНІ ПИТАННЯ ДЛЯ
САМОПІДГОТОВКИ
1.
Методи обробки отворів.
2.
Інструмент для обробки отворів.
3.
Верстати, на яких обробляють отвори.
4.
Операції, які виконуються на
свердлильних верстатах.
5.
Особливості обробки глибоких отворів.
6.
Точність і якість поверхні отворів,
оброблених різними способами.
7.
Елементи режиму різання при свердленні,
зенкеруванні, розвертанні.
8.
Порядок призначення елементів режиму
різання.
9.
Особливості обробки отворів у великих та
важких деталях.
10.
Операції, які виконуються на радіально –
свердлильних верстатах.
|