Мета роботи: ознайомитись з будовою, органами
управління токарно-гвинторізного верстата; набути практичних навичок
з налагодження, настроювання токарного верстата і обробки на ньому
різних поверхонь.
1 ТЕОРЕТИЧНІ ВІДОМОСТІ
Точінням називається
високопродуктивний технологічний метод обробки поверхонь, головним
чином поверхонь обертання різної форми (циліндричних, конічних,
фасонних), а також плоских (торцевих) токарними різцями на токарних
верстатах.
1.1 Токарні верстати
Основними розмірними
характеристиками токарних верстатів є висота центрів над напрямними
станини і відстань між центрами. Висота центрів над станиною
визначає найбільший діаметр заготовки, яку можна обробляти на
верстаті, а відстань між центрами найбільшу її довжину.
Токарно-гвинторізні верстати
поділяються на дрібні з висотою центрів до 150 мм, середні з
висотою центрів 150 ... 300 мм і великі з висотою центрів
більше 300 мм.
На токарно-гвинторізних
верстатах можна виконувати такі роботи:
- точіння зовнішніх і
внутрішніх циліндричних і конічних поверхонь;
- точіння торцевих поверхонь;
- свердління, зенкерування,
розвертання і розточування отворів;
- нарізання зовнішніх і
внутрішніх різьб різцем, плашкою, гайкорізом;
- точіння фасонних і сферичних
поверхонь;
- обкатування поверхонь
роликами і накатування рифлень.
Незалежно від розмірів і
конструктивних особливостей всі токарно-гвинторізні верстати мають
загальні вузли і механізми (рис. 36).
Станина 1 служить для з'єднання
всіх основних вузлів і частин верстата. На ній встановлені передня
бабка 3, коробка подач 2, задня бабка 11 і супорт. Передня бабка
розташована зліва на станині. Вона має чавунний корпус, всередині
якого розміщена коробка швидкостей 4 і пустотілий шпиндель 5.
Коробка швидкостей надає обертання шпинделю і дозволяє змінювати
частоту і напрям обертання. На правому кінці шпинделя встановлюється
пристрій 6 для закріплення заготовки, яка оброблюється (патрон,
планшайба тощо). Задня бабка 11 встановлюється на правому кінці
станини і може пересуватися по її напрямних. Вона використовується
для закріплення різального інструменту (свердел, зенкерів,
розверток) або заднього центра.
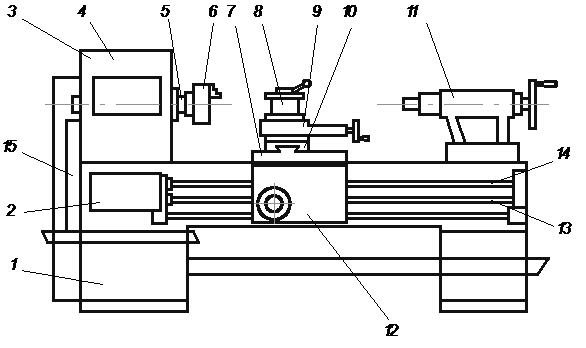
Рисунок 35 –
Загальний вигляд токарно-гвинторізного верстата
Поздовжній супорт 7
пересувається по напрямних станини і забезпечує поздовжню подачу.
Поперечний супорт 10 пересувається по напрямних поздовжнього
супорта перпендикулярно до осі обертання шпинделя. На ньому
змонтований верхній супорт 9 з різцетримачем 8.
Пересування супортів
визначається за допомогою лімбів, які являють собою циліндричні
барабани з нанесеними на них поділками. Ціна поділки лімба, тобто
величина переміщення супорта при повороті рукоятки ручної подачі на
одну поділку, характеризує точність верстата.
Коробка подач 2
дозволяє змінювати частоту обертання ходового вала 13 або ходового
гвинта 14, отже і величину подачі. Коробка подач з'єднана зі
шпинделем гітарою змінних зубчастих коліс 15.
Механізми, що розташовані у
фартусі супорта 12, перетворюють обертальний рух ходового гвинта або
ходового вала в прямолінійний поступальний рух поздовжнього або
поперечного супортів. При нарізанні різьби використовується ходовий
гвинт, а при всіх інших видах токарної обробки - тільки ходовий вал.
1.2 Рухи при токарній обробці
Рухи, які виконують інструмент
і заготовка в процесі різання, називаються робочими. Для будь-якого
металорізального верстата робочими рухами є рух різання (головний
рух) і рух подачі.
Рух різання для токарного
верстата - це обертання заготовки. Він забезпечує зняття стружки з
заготовки.
Рух подачі забезпечує поздовжнє
або поперечне переміщення різального інструмента відносно заготовки
(рис. 36) .
Рух різання визначається
швидкістю різання, яка вимірюється в метрах за хвилину і може бути
розрахована за формулою:
V =
pDn
/ 1000 ,
де
D - діаметр
оброблюваної заготовки в мм;
n
- частота обертання заготовки в обертах за хвилину.
Рух подачі визначається шляхом,
пройденим інструментом відносно заготовки за її один оберт, і
вимірюється в мм/об.
1.3 Режим різання
Під режимом різання розуміють
сукупність показників, які визначають продуктивність процесу різання
та якість оброблюваних поверхонь. До основних показників режиму
різання відносять швидкість різання V, подачу
S та глибину різання
(рис. 36). Глибиною різання називають
відстань між оброблюваною і обробленою поверхнями за один робочий
хід інструмента відносно поверхні, яка обробляється.
Призначення елементів режиму різання відбувається у такій
послідовності: спочатку вибирається максимально можлива і доцільна
глибина різання
t,
потім максимально можлива подача
S,
а потім вже підраховується з урахуванням оптимальної стійкості
інструмента і інших конкретних умов обробки швидкість різання. Для
призначення елементів режиму різання необхідно знати матеріал
заготовки і його фізико-механічні властивості; розміри заготовки,
розміри деталі і технічні умови на її оброблені поверхні; матеріал і
геометричні елементи ріжучої частини інструмента, його розміри,
максимально допустимий знос і стійкість; кінематичні і динамічні
дані верстата, на якому будуть обробляти дану заготовку.
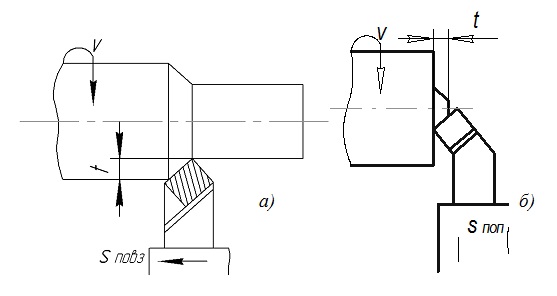
Рисунок 36 –
Схеми робочих рухів при токарній обробці:
а
– з поздовжньою подачею; б – з поперечною подачею
Глибина різання визначається
величиною припуску на обробку. При чорновій обробці припуск доцільно
видаляти за один прохід. В цьому випадку глибина різання дорівнює
припуску на обробку. При зрізанні підвищених припусків або при
роботі на малопотужних верстатах припуск інколи доводиться розбивати
на частини, роблячи уже кілька проходів.
При напівчистовій обробці
глибина різання призначається в межах 0,5 ... 2,0 мм, а при
чистовій - в межах 0,1 ... 0,4 мм.
Подачу доцільно призначати
максимально можливою з метою підвищення продуктивності праці з
урахуванням всіх факторів, що впливають на її величину.
На практиці подача звичайно
надається з таблиць довідників з режимів різання, складених на
основі досвіду роботи передових машинобудівних заводів. При чорновій
(грубій) обробці максимальну подачу можуть обмежувати міцність і
жорсткість різального інструменту, заготовки, міцність деталей
механізмів верстата.
При напівчистовій і чистовій
обробці максимальну подачу обмежують вимоги до якості обробленої
поверхні, тому що чим більша подача, тим більш шорстка оброблена
поверхня.
Після визначення глибини
різання і подачі при відомій стійкості інструменту визначається
швидкість різання V за формулами, що наводяться у довідниках
з режимів різання.
1.4 Токарні різці і їх
застосування
Для обробки заготовки на
токарно-гвинторізних верстатах застосовують різноманітні різці, які
класифікують за різними ознаками.
За матеріалом різальної частини
розрізняють різці з швидкорізальної сталі, твердосплавні
(металокерамічні) і мінералокерамічні.
За конструкцією різці поділяють
на суцільні і складені. У складених різців різальна частина являє
собою пластинку із швидкорізальної сталі, твердого сплаву або іншого
високоякісного інструментального матеріалу, яка з'єднана механічно,
зварюванням або паянням з державкою різця, що виконана з вуглецевої
сталі.
За розташуванням головної
різальної кромки різці поділяють на праві і ліві. Правим називається
різець 2 (рис. 37), у якого головна різальна кромка знаходиться з
боку великого пальця правої руки, накладеної долонею зверху на
різець таким чином, що пальці напрямлені до вершини різця. На
верстаті такі різці (9, 10) працюють при подачі справа наліво (до
передньої бабки). Лівим називають різець 1, у якого головна
різальна кромка знаходиться з боку великого пальця лівої руки. На
верстаті він працює при подачі зліва направо (різець 4).
За виглядом осі різця в плані
розрізняють різці прямі 4 і відігнуті 9 (див. також рис. 36,
відповідно а і б).
За характером обробки різці
поділяють на обдирні (чорнові) і чистові.
За призначенням токарні різці
поділяють на прохідні, підрізні, відрізні, розточні, різьбові,
канавні, фасонні.
Прохідні різці призначені для
обточування зовнішніх поверхонь тіл обертання і для підрізання
торцевих поверхонь. Прохідні прямі різці використовують головним
чином для обробки зовнішніх 4 (рис. 36) поверхонь.
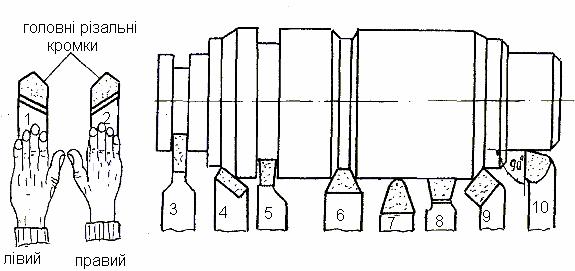
Рисунок 36 – Основні види
різців
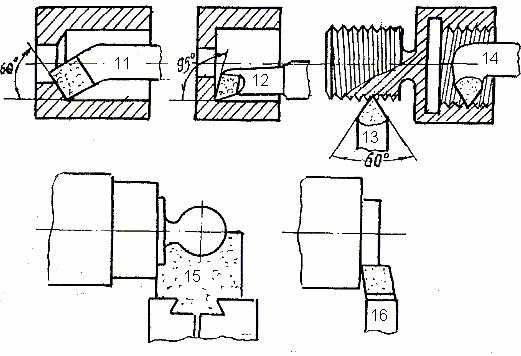
Рисунок 37 –
Типи токарних різців
Прохідні відігнуті різці більш
універсальні, тому що ними можна обробляти як зовнішні поверхні тіл
обертання (9, рис. 36), так і підрізати торець (рис. 36, 6).
Прохідні упорні різці 10 (рис.
36) з головним кутом у плані, що дорівнює 90°, застосовують для
деталей, у яких обробка циліндричної поверхні повинна бути закінчена
підрізкою невеликого уступу.
Для чистової обробки
застосовують різці двох типів: з закругленою вершиною (7, рис. 36) і
широкі чистові 8 з прямолінійною головною різальною кромкою. Перші
застосовують при обробці невеликих деталей, другі – великих.
Підрізні торцеві різці 16
(рис. 37) застосовують
для обробки торцевих площин.
Відрізні різці 3 застосовують
для розрізання заготовки.
Розточувальні різці прохідні 11
та упорні 12 призначені для розточування відповідно наскрізних і
глухих отворів.
Різьбові різці 13 та 14
застосовують для нарізання на заготовках відповідно зовнішніх і
внутрішніх різьб. Форма різальної частини різця повинна відповідати
формі профілю різьби (трикутна з кутами 60° і 55°, трапецеїдальна,
прямокутна та ін.).
Фасонними різцями 15 обробляють
фасонні поверхні.
Канавкові різці 5, 6
застосовують для прорізання канавок різного профілю.
2 ОСНОВНІ РОБОТИ, ЩО
ВИКОНУЮТЬСЯ НА ТОКАРНО–ГВИНТОРІЗНИХ ВЕРСТАТАХ
2.1 Обробка циліндричних
поверхонь
Циліндричні поверхні обробляють
при поздовжньому переміщенні поздовжнього супорта або верхнього
супорта. Зовнішні циліндричні поверхні обробляють звичайно
прохідними різцями, а внутрішні розточувальними. Пристосування для
закріплення заготовок вибирають залежно від їх форми і розмірів.
Заготовку типу вал залежно від відношення її довжини до діаметра
рекомендується закріплювати так:
при
l/d
< 4 - в патроні;
при 4
³
l/d
< 10 - в центрах;
при
l/d > 10...12
- в центрах з додатковою опорою заготовки на кулачки рухомого або
нерухомого люнета.
2.2 Обробка конічних поверхонь
Конічні поверхні на токарному
верстаті можуть бути оброблені одним з таких методів:
- різцем з похило розташованою
різальною кромкою;
- за допомогою повороту
верхньої каретки супорта (верхнього супорта);
- зміщенням задньої бабки;
- за допомогою копіювальної
лінійки.
Різцем з похило розташованою
різальною кромкою обробляють зовнішні 1 і внутрішні 2 конічні
поверхні (рис. 38, а), довжина яких не перевищує 20 ... 25
мм.
За допомогою повороту верхнього
супорта обробляють зовнішні і внутрішні конічні поверхні, довжина
яких не перевищує довжини ходу верхнього супорта. Напрямні верхнього
супорта встановлюють під кутом
j (6,
рис. 38, г) до осі обертання заготовки, який дорівнює
половині кута при вершині оброблюваного конуса. Подача різця
здійснюється вручну.
Методом зміщення корпусу
задньої бабки обробляють тільки зовнішні конічні поверхні, у яких
довжина твірної порівняно велика, а кут при вершині конуса не
перевищує 10 ... 12о. Заготовку в цьому випадку
закріплюють у центрах, а корпус задньої бабки зміщують в поперечному
напрямі на величину h
(рис. 38, в):
h =
L×sin
j,
де
L - довжина
заготовки, мм;
j
- половина кута при вершині конуса.
За допомогою копіювальної
лінійки можна обробляти зовнішні і внутрішні конічні поверхні
великої довжини, кут при вершині у яких не перевищує 25°.
На рис. 38, г показано
будову однієї з конструкцій конусної лінійки.
Основою конусної лінійки
служить кронштейн 5, прикріплений болтами до поздовжніх полозків
супорта; в кронштейні є поздовжні напрямні у вигляді ластівчиного
хвоста для основи лінійки 7. В основу лінійки вкручений стержень 8,
який другим кінцем входить в отвір кронштейна 10 і закріплюється в
ньому болтом 9.
Кронштейн 10 за допомогою
болтів 11 закріплюють на станині верстата. На
верхній площині основи лінійки встановлена конусна лінійка 1,
в якій зроблено прямокутний паз 6. В пазу знаходиться повзунок 2, з
яким за допомогою болта 4 з'єднана тяга 3, другий кінець тяги
гвинтами з'єднаний з поперечними полозками супорта.
При користуванні конусною
лінійкою поперечні полозки відокремлюють від гвинта поперечної
подачі, для чого звичайно гвинт поперечної подачі виймають із
супорта. Конусну лінійку встановлюють за однією з шкал, нанесених на
кінцях основи лінійки, на кут
j,
який дорівнює половині кута при вершині конуса, що обробляється, і
закріплюють болтами. При поздовжньому автоматичному або ручному
переміщенні супорта повзунок 2 і різець переміщуються паралельно
твірній оброблюваного конуса. Необхідну глибину різання встановлюють
ручним переміщенням верхнього супорта.
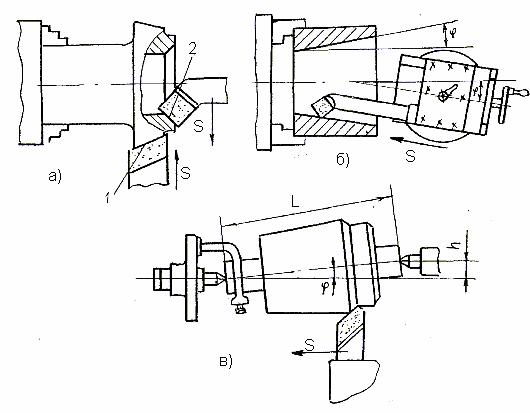
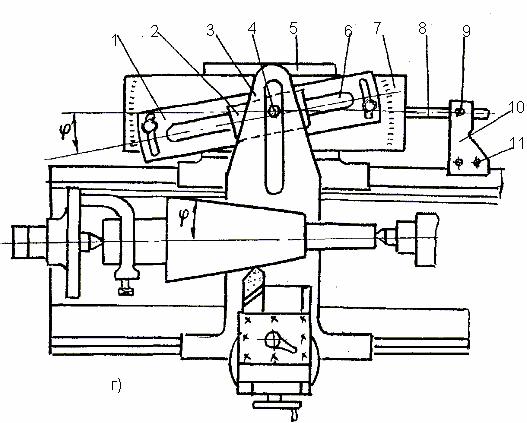
Рисунок 38 –
Схеми обробки конічних поверхонь на токарних верстатах
2.3 Нарізання різьби
На токарно-гвинторізних
верстатах можна нарізати різні типи різьби у великому діапазоні їх
кроків за допомогою токарних різців. Перед нарізанням різьби
механізм подачі верстата настроюють таким чином, щоб за кожний оберт
шпинделя, а отже, і заготовки, різець разом з супортом (який дістає
в цьому випадку рух від ходового гвинта) переміщувався б на величину
кроку різьби. Це досягається за допомогою коробки подач та гітари.
При необхідності нарізання різьби підвищеної точності коробка подач
відокремлюється від механізму подачі, а необхідний крок різьби
забезпечується настройкою тільки однієї гітари змінних зубчастих
коліс.
На рис. 37 показана схема
нарізання зовнішньої і внутрішньої різьб відповідно різцями 13 і 14.
2.4 Обробка фасонних поверхонь
Фасонні поверхні 2 невеликої
довжини на заготовці 1 обробляють фасонним різцем, застосовуючи
тільки поперечну подачу (рис. 39, а).
Фасонні поверхні великої
довжини обробляють за допомогою копіра. Призначення копіра: передати
різцю за допомогою спеціальної слідкувальної системи поперечне
переміщення, погоджене з його поздовжнім переміщенням. Застосовують
різні слідкувальні системи: механічну, гідравлічну, електромеханічну
та ін. Як приклад на рис. 39, б показана схема обробки
фасонної поверхні 2 за допомогою копіра 5 з механічною слідкувальною
системою. Копір 5 закріплений на кронштейні 6, який болтами
прикріплений до станини верстата. В копірі зроблено криволінійний
паз за формою твірної поверхні, що обробляється. В паз входить ролик
7, вільно насаджений на осі 4, яка закріплена в тязі 3, з'єднаній
жорстко з поперечними полозками супорта. Гвинт поперечної подачі
повинен бути відокремлений від поперечних полозків. При поздовжньому
переміщенні супорта ролик котиться по криволінійному пазу і
механічно через тягу переміщує в поперечному напрямі супорт разом з
різцем 1, вершина якого при цьому переміщується еквідистантно
криволінійній твірній поверхні, що оброблюється. Встановлюють різець
на глибину різання за допомогою верхніх полозків, для чого
поворотний круг закріплюють так, щоб напрямні верхніх полозків були
перпендикулярні до напрямних станини.
3 ХІД РОБОТИ
1.
Вивчити принцип
роботи та будову токарно-гвинторізного верстата: розташування та
призначення головних вузлів та механізмів, рукояток управління.
2.
Вивчити
конструкцію та типи токарних різців, їх призначення.
3.
Вивчити методи
обробки різних поверхонь на токарних верстатах.
4.
Виконати точіння
заготовки діаметром
D,
розрахувавши за вказаною швидкістю різання необхідну частоту обертів
шпинделя. За виміряним часом обробки знайти подачу.
5.
Скласти звіт.
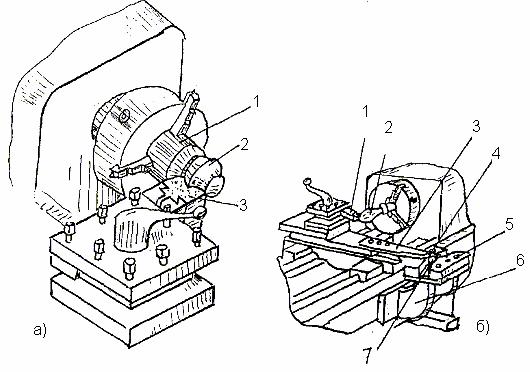
Рисунок 39 –
Схеми обробки фасонних поверхонь
на токарному верстаті
різцем:
а
– фасонним; б
– прохідним за допомогою копіювальної
лінійки
4 ЗМІСТ ЗВІТУ
Звіт з лабораторної роботи
повинен містити:
1.
Короткі теоретичні відомості про обробку
на токарних верстатах;
2.
Загальний вигляд токарно-гвинторізного
верстата з позначеннями. Ескізи токарних різців і схеми обробки
різних поверхонь;
3.
Розрахунки частот обертання шпинделя,
подачі (або швидкості різання і часу обробки за вказаними частотою
обертання і подачею);
4.
Висновки.
5 КОНТРОЛЬНІ ПИТАННЯ ДЛЯ
САМОПІДГОТОВКИ
1.
Призначення токарних верстатів. Типи
токарних верстатів.
2.
Призначення основних вузлів і механізмів
токарно-гвинторізного верстата. Рухи при токарній обробці.
3.
Режим різання при точінні.
4.
Порядок розрахунку елементів режиму
різання при точінні.
5.
Методи обробки конічних поверхонь на
токарних верстатах.
6.
Методи нарізання різьби на
токарно-гвинторізних верстатах.
7.
Способи закріплення заготовок на
токарних верстатах.
8.
Методи обробки фасонних поверхонь на
токарних верстатах.
|