1) вибір і обґрунтування вихідних даних для формування програми ТО і ремонту автомобілів;
2) варіантний пошук раціональних режимів ТО і ремонту автомобілів в конкретних умовах експлуатації;
5) розрахунок чисельності виробничого персоналу, допоміжних робітників.
2.1.2 Проектування організаційно-виробничої структури управління процесами ТО і ремонтом автомобілів.
1) варіантний пошук оптимальних методів організації ТО і ремонту рухомого складу, параметрів роботи зон і дільниць;
3) визначення площ виробничо-складських приміщень, зон зберігання і допоміжних приміщень.
1) розроблення схеми організації ТО і ПР автомобілів і графіка виробничого процесу АТП;
3) розроблення плану виробничого корпусу (на основі варіантного пошуку).
2.2 Організація ТО і ремонту автомобілів на робочих постах і спеціалізованих виробничих дільницях.
2.2.1 Характеристика підрозділу.
2.2.2 Розроблення технологічного процесу робіт у зоні або дільниці (на основі варіантного пошуку).
2.2.3 Розподіл об’ємів робіт і виконавців по постах, робочих місцях і кваліфікації.
2.2.4 Обґрунтування і вибір технологічного обладнання (на основі варіантного пошуку).
2.2.5 Уточнення розрахунку площі виробничого підрозділу (з використанням габаритних розмірів технологічного обладнання).
2.2.6 Розроблення планувального рішення виробничого підрозділу (на основі варіантного пошуку).
2.2.7 Розрахунок рівня та ступеня механізації робіт.
2.2.8 Розроблення (на основі варіантного пошуку) і оформлення технологічної карти виробничого процесу на дільниці.
2.3 Проектування (модернізація) конструкції технологічного обладнання.
3) вибір типової конструкції, на основі якої проводиться проектування (модернізація) конструктивних елементів;
4) вибір та обґрунтування вузла, який буде проектуватися (модернізуватися).
1) виявлення можливих варiантiв конструкторських рішень (принципи дії, принципові схеми, компоновки вузлів та агрегатів);
2) перевірка варiантiв на вимоги роботоздатностi, техніки безпеки, виробничої санiтарiї, експлуатаційної та ремонтної ефективності (по-рівняльна оцінка варiантiв);
3) вибір та обґрунтування оптимального варіанта проектування.
3) визначення основних геометричних характеристик.
2.3.4 Особливості монтажу, налагодження, пуску та експлуатації ТОБ.
2.3.5 Розроблення технологічного процесу функціонування обладнання, викладення переліку основних робіт з підтримки обладнання в роботоздатному стані.
1. Вибір і обґрунтування вихідних даних. До вихідних даних для розрахунку виробничої програми належать:
– умови зберігання рухомого складу.
Залежно від задач проектування конкретного підприємства зміст і повнота вихідних даних можуть бути різними. При будівництві нових АТП відомі лише річний обсяг і види вантажів, що перевозяться, або чисельність жителів у населеному пункті. При розробленні проектів реконструкції, технічного переозброєння і розширення звичайно відомі тип і кількість рухомого складу, всі інші необхідні показники та умови роботи підприємства. Обґрунтування вихідних даних полягає в їхньому кількісному визначенні та прив’язці до конкретного об’єкта згідно з нормативно-технічною документацією чи з показниками, отриманими в результаті узагальнення досвіду роботи передових підприємств галузі.
Тип і кількість рухомого складу та середньодобові пробіги визначаються на стадії техніко-економічного обґрунтування; дорожньо-кліматичні умови експлуатації та умови зберігання автомобілів визнаються та обґрунтовуються на основі рекомендацій «Положення про технічне обслуговування і ремонт ДТЗ», ОНТП 01-91 та СНиП 21-02-99 [25, 28, 29, 43].
2. Пошук раціональних режимів ТО і ремонту автомобілів визначається на основі варіантного пошуку з урахуванням рекомендацій ОНТП 01-91. На основі розробленого режиму роботи рухомого складу та конкретних умов експлуатації рухомого складу (години виїзду і повернення рухомого складу, тривалість пікового випуску та повернення тощо) розробляється кілька варіантів режимів роботи виробничих підрозділів, визначаються години роботи та тривалість змін відповідних зон та дільниць. Серед розроблених варіантів вибирається оптимальний та розробляється сумісний графік роботи автомобілів на лінії та виробничих підрозділів.
Після виконання розрахунків виробничої програми режим роботи виробничих підрозділів може бути скоригований.
3. Коригування нормативів технічного обслуговування в ремонту рухомого складу.
Виробничу програму та обсяг робіт з ТО й ремонту розраховують, користуючись такими нормативами: пробіг рухомого складу до капітального ремонту; періодичність ТО; трудомісткість ТО і поточного ремонту; простої рухомого складу в КР, ТО і ПР. Ці нормативи наведено в ОНТП 01-91 [25].
Проте зазначені нормативи встановлено для першої категорії умов експлуатації, базових моделей автомобілів, помірного кліматичного району; автотранспортних підприємств, на яких здійснюються ТО й ремонт 200-300 од. рухомого складу, що складають три технологічно сумісні групи, відкритого способу зберігання. Оснащення АТП засобами механізації відповідало табелю технологічного устаткування. Якщо автомобілі працюють в умовах, що відрізняються від зазначених, нормативи коригують, ураховуючи конкретні умови експлуатації та особливості АТП, яке проектують. Для цього користуються коефіцієнтами, які враховують такі фактори:
З метою проектування коригування нормативів залежно від пробігу рухомого складу з початку експлуатації не проводиться.
Результуючий коефіцієнт коригування нормативів визначається як добуток окремих коефіцієнтів для таких показників:
4. Розрахунок річної та добової програми з ТО та ПР рухомого складу.
Виробнича програма підприємств з ТО характеризується числом технічних впливів, запланованих на певний період. План АТП з основних показників установлюють на календарний рік. Тому виробничу програму з ТО також розраховують на рік. Окрім того, щоб вибрати метод організації ТО, визначають також і добову програму.
Виробничу програму з ТО розраховують різними методами. Великого поширення набули цикловий метод розрахунку (за цикл узято пробіг до КР) і розрахунок за річнім пробігом. Щоб визначити річну виробничу програму, найдоцільніше скористатися методом розрахунку за річнім пробігом.
Капітальний ремонт агрегатів і вузлів вантажних і легкових автомобілів, а також капітальний ремонт автобусів на базі готових агрегатів в автотранспортних підприємствах, не проводиться, його виконання слід передбачати за допомогою кооперації зі спеціалізованими авторемонтними підприємствами.
Розрахунок програми при різнотипному парку виконують за групами одномарочного рухомого складу. ТО автопоїздів звичайно здійснюють, не розчіплюючи тягач і причіп. Тому програму для автопоїздів розрахують як для цілої одиниці рухомого складу.
Діагностування Д-1 призначено для визначення технічного стану агрегатів, вузлів і систем, які забезпечують безпеку руху. Д-1 виконують з періодичністю ТО-1; воно передбачається після ТО-2 і ПР по рядах, які забезпечують безпеку руху. Згідно з дослідними даними кількість автомобілів, які діагностуються при ПР дорівнює 10% річної програми ТО-1.
Діагностування Д-2 потрібне для визначення потужнісних і економічних показників автомобілів і обсягів ПР. Д-2 виконують з періодичністю ТО-2, а іноді при ПР. Кількість автомобілів, що діагностуються при ПР, дорівнює 20% річної програми ТО-2.
Річний обсяг робіт на АТП обчислюють у людино-годинах. Він містить обсяги робіт ЩО, ТО-1, ТО-2, ПР і самообслуговування підприємства. Обсяги ЩО, ТО-1, ТО-2 визначають на основі річної виробничої програми й трудомісткості обслуговування даного виду. Обсяг ПР визначають виходячи з річного пробігу автомобілів і питомої трудомісткості ПР на 1000 км пробігу. Сезонне ТО, що виконується двічі на рік, як правило, суміщають з ТО-2 і як окремий вид обслуговування не враховують.
Розподіл річного обсягу робіт ТО і ПР автомобілів за видами робіт виконується на основі рекомендацій ОНТП 01-91.
Під час організації ТО-2 виникає необхідність в знятті окремих приладів і вузлів для усунення несправності і контролю на спеціальних стендах на виробничих дільницях. В основному це роботи, які пов’язані з системою живлення, електротехнічні, акумуляторні і шиномонтажні. Тому виконання 90-95% обсягу робіт ТО-2 планується на постах, а 5-10% – на виробничих дільницях. В практиці проектування цей обсяг робіт розподіляється рівномірно по відповідних дільницях.
При організації Д-1 і Д-2 на самостійних дільницях трудомісткість діагностичних робіт визначають у частках трудомісткості ТО й ПР.
Частки трудомісткості ТО-1, ТО-2 і ПР, що припадають на діагностичні роботи, наведено в ОНТП 01-91. Відповідно річні обсяги робіт, які виконуються в зонах ТО-1 і ТО-2, зменшуються на відповідні величини, і відповідно становлять:
5. Розрахунок чисельності виробничого персоналу та допоміжних робітників.
Залежно від виду виконуваних робіт розрізняють виробничих і допоміжних робітників. До виробничих належать робітники зон і дільниць, які безпосередньо виконують роботи з ТО і ПР рухомого складу. Розрізняють технологічно необхідну (явочну)
і штатну (облікову)
чисельність робітників.
Технологічно необхідна чисельність робітників забезпечує виконання добової виробничої програми і визначається так:
Штатна чисельність робітників забезпечує виконання річних обсягів робіт з ТО й ремонту рухомого складу:
Річній фонд часу робочого місця визначається кількістю робочих днів протягом року і тривалістю зміни залежно від тривалості робочого тижня. У практиці проектування для розрахунку явочної чисельності робітників приймають
год для виробництв з нормальними умовами праці і 1830 год для виробництв зі шкідливими умовами.
Технологічно необхідну і штатну кількість ремонтних робітників розраховують для кожного з виробничих підрозділів, створюваних з урахуванням видів і трудомісткості робіт.
Якщо річний обсяг окремих видів робіт незначний (значно менший ніж 2000 люд.-год), потрібно створювати об’єднаний підрозділ для робітників споріднених спеціальностей. Наприклад, можна об’єднати шиноремонтну і вулканізаційну дільниці, деревообробну і оббивну, арматурну і бляхарську тощо. Якщо робочих місць більше двох, створюють спеціалізовану дільницю.
Чисельність допоміжних робітників АТП, які зайняті на роботах із самообслуговування підприємства та на інших роботах, беруть у процентному відношенні від штатної чисельності виробничих робітників. Норми та розподіл чисельності допоміжних робітників за видами робіт наведений в ОНТП 01-91.
Чисельність персоналу управління і службовців та їх розподіл за професіями приймають залежно від потужності АТП і типу рухомого складу згідно з рекомендаціями, наведеними в ОНТП 01-91. Чисельність персоналу виробничо-технічної служби вибирають залежно від чисельності виробничих робітників і кількості автомобілів на підприємстві.
Для виробничих автотранспортних об’єднань, як правило, в одній із виробничих філій слід передбачати центральний апарат управління – загальне керівництво, планово-виробничий відділ, відділ праці і заробітної платні, бухгалтерію, відділ матеріально-технічного постачання, відділ кадрів, адміністративно-господарський відділ, відділ головного механіка, виробничо-технічний відділ, відділ управління виробництвом і відділ технічного контролю чисельністю, розрахований на кількість і об’єм робіт ТО і ПР рухомого складу, агрегатів, вузлів, деталей, молодший обслуговуючий персонал і пожежно-сторожова охорона.
В експлуатаційних філіях виробничих об’єднань слід передбачати керівництво філією, відділ експлуатації, диспетчерську і гаражну служби чисельністю, розрахованою на кількість закріпленого за філією рухомого складу, персонал управління виробництвом і технічного контролю, розрахований на кількість і об’єм робіт ТО і ПР рухомого складу, молодший обслуговуючий персонал і пожежно-сторожова охорона.
Визначившись зі складом персоналу управління розробляється структура і управління технічної служби АТП та складається схема організаційно-виробничої структури управління процесами ТО і ремонту автомобілів.
Рекомендації з розроблення організаційно-виробничої структури управління процесами ТО і ремонту автомобілів детально розглянуті в [11, 12].
1. Вибір методу організації ТО і ПР автомобілів, режимів роботи виробничих підрозділів виконується на основі варіантного пошуку.
Розрізняють два методи організації ТО автомобілів: одиничний і потоковий.
Організація одиничного методу обслуговування значно простіша, ніж на потокових лініях. Так, при обслуговуванні на універсальних постах, на них можливо виконання неоднакового об’єму робіт. Наприклад, при ТО автомобілів різних моделей, при суміщенні з ТО супутнього ПР різного об’єму. З іншого боку використання цього методу призводить до значних втрат часу на встановлення автомобілів на пости та з’їзд з них, забруднення повітря відпрацьованими газами при маневруванні автомобілів при виїзді або з’їзді з поста, необхідності дублювання обладнання, використання робітників-універсалів більш високої кваліфікації, що збільшує витрати на проведення ТО.
Найпрогресивнішим методом організації ТО є виконання його на потокових лініях. Потокова організація ТО забезпечує:
– скорочення трудомісткості робіт і підвищення продуктивності праці за рахунок спеціалізації виробничих постів, місць і виконавців;
– підвищення ступеня використання технологічного обладнання і оснащення внаслідок проведення на кожному посту одних і тих самих операцій;
– підвищення трудової і виробничої дисципліни внаслідок неперервності та ритмічності виробництва;
– покращення умов праці виконавців і скорочення виробничої площі.
Для організації виробництва потоковим методом необхідні певні умови. До них відносяться:
виконання ПР перед поставленням автомобілів в ТО-1 і ТО-2.
Як правило, з регламентними роботами ТО виконуються операції супутнього ПР, які можуть порушувати ритмічність роботи потокових ліній. Тому в цілях забезпечення якості виконання профілактичних робіт ТО, рівномірного завантаження виконавців і підвищення продуктивності праці об’єм супутніх робіт ПР, які виконуються при ТО, обмежується. Сумарна трудомісткість операцій супутнього ПР не повинна перевищувати 15-20% трудомісткості відповідного виду ТО при виконанні робіт на потокових лініях і 30% – при виконанні робіт на окремих постах.
В принципі доцільність використання того чи іншого методу організації ТО в основному визначається числом постів, тобто залежить від добової (змінної) програм і тривалості впливу. Тому як основний критерій для вибору методу ТО можуть служити добова (змінна) виробнича програма відповідного виду ТО або розрахункова кількість виробничих постів.
Мінімальна добова (змінна) програма, при якій доцільний потоковий метод ТО, рекомендована Положенням і складає: для ТО-1 – 12-15, а для ТО-2 5-6 технологічно сумісних автомобілів. При меншій програмі ТО-1 і ТО-2 проводяться на окремих спеціалізованих і універсальних постах. При визначенні методу організації на основі кількості виробничих постів приймають потоковий метод для ТО-1 і загальної діагностики одиночних автомобілів при розрахунковій кількості 3 і більше постів, для автопоїздів – 2 і більше постів; для ТО-2 одиночних автомобілів – 4 і більше постів, автопоїздів – 3 і більше постів.
Діагностування рухомого складу на АТП може проводитись окремо або суміщатись з ТО і ПР. Форми організації діагностування залежать від потужності АТП, типу рухомого складу, його різномарочності, засобів діагностування, що використовуються, наявності виробничих площ і визначають розміщення діагностичного обладнання за видами ТО і діагностування.
На невеликих АТП зі списочним складом до 150 технологічно сумісних автомобілів і при змішаному парку всі види діагностування рекомендується проводити на окремій діагностичній дільниці, оснащеній комбінованим діагностичним стендом або сумісно з ТО та ПР переносними приладами.
Для середніх АТП з числом 150-200 і більше автомобілів доцільно пости Д-1 і Д-2 мати роздільними. Для великогабаритного рухомого складу, при реконструкції АТП і обмежених виробничих площах, а також при організації ТО-1 на потокових лініях Д-1 рекомендується проводити сумісно з ТО-1.
Для великих АТП з числом автомобілів більше 400 і при наявності високопродуктивних, автоматизованих діагностичних засобів Д-1 і Д-2 проводяться на окремих спеціалізованих дільницях. При цьому, крім постів Д-1 і Д-2, необхідно мати пости та засоби діагностування в зоні ПР (стенди для та регулювання гальм і кутів встановлення керованих коліс).
Прибирально-мийні роботи рухомого складу можуть проводитись як на окремих постах, так і на потокових лініях. На невеликих підприємствах ці роботи проводяться на тупикових або проїзних постах. Якщо автомобілів на АТП більше 50, виконання мийних робіт передбачається механізованим способом. Потокові лінії використовуються, як правило, на середніх і великих АТП при одночасному використанні механізованих установок для миття і сушіння рухомого складу.
Постові роботи ПР можуть виконуватись на універсальних і спеціалізованих (паралельних) постах.
Метод універсальних постів передбачає виконання робіт на одному посту бригадою ремонтних робітників різних спеціальностей або робочим-універсалом високої кваліфікації, а метод спеціалізованих постів – на декількох постах, призначених для виконання певного виду робіт (двигун, трансмісія і ін.).
При числі постів ПР більше 5-6 їх спеціалізують за видами робіт. При цьому розподіл постів за їх спеціалізацією (в відсотках від загального числа постів) наведено в таблиці 5.38.
Таблиця 5.38 – Спеціалізація постів ПР за видами робіт
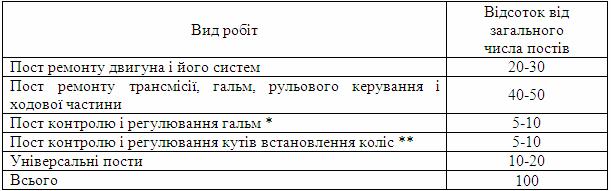
Примітки:
1. * При числі постів 10 і більше.
2. ** При числі постів більше 15.
Режим роботи зон ТО і ПР характеризується числом робочих днів на рік, тривалістю роботи (числом робочих змін, тривалістю і часом початку та кінця зміни), розподіл виробничої програми за часом її виконання. Число робочих днів зони залежить від числа днів роботи рухомого складу на лінії і виду ТО. В свою чергу, тривалість роботи зон залежить від добової виробничої програми і часу, протягом якого може виконуватись даний вид ТО і ПР.
При необхідності можливе коригування змінності роботи зон та дільниць, визначених в 2.1.1.
Режим роботи зони повинен бути узгодженим з графіком випуску і повернення автомобілів з лінії (рис. 5.7).
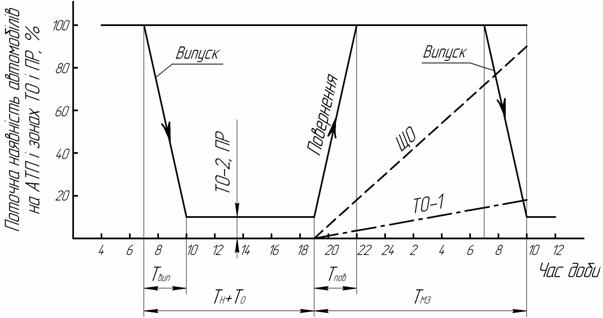

Рисунок 5.7 – Добовий графік випуску і повернення автомобілів на АТП
Графік дає наглядне уявлення про число автомобілів, які знаходяться на лінії і на АТП в будь-який час доби, що дозволяє встановити найраціональніший режим роботи зон ТО автомобілів. Якщо автомобілі працюють на лінії 1; 1,5 або 2 робочих зміни, то ЩО і ТО-1 в час доби, який залишився (міжзмінний час).
Міжзмінний час – це період між поверненням першого автомобіля і випуском останнього. При рівномірному випуску автомобілів тривалість міжзмінного часу
.
Режим роботи дільниць діагностування залежить від режиму роботи зон ТО і ПР. Дільниця діагностування Д-1 звичайно працює одночасно з зоною ТО-1. Діагностування Д-1 після ТО-2 проводять в денний час. Дільниця поелементної (поглибленої) діагностики Д-2 працює в одну або дві зміни.
Добовий режим зони ПР складає дві, а іноді і три робочі зміни, з яких одну (зазвичай денну) зміну працюють всі виробничо-допоміжні дільниці і пости ПР. В робочі зміни, які залишились, виконуються постові роботи з ПР автомобілів, виявлені при ТО, діагностуванні або за заявкою водія.
При проектуванні нових АТП слід враховувати, що використання подовжених змін або півторазмінної роботи виконавців, як правило, не допускається органами санітарної інспекції і охорони праці, незалежно від способу компенсації за перепрацьований час.
2. Розрахунок кількості постів (ліній) ТО і ПР.
Мінімальна кількість робочих постів за видами робіт ЩОд, окрім механізованих мийних, розраховується за формулою:
, (5.56)
де
– річний об’єм ЩОд, люд.-год;
– процентне відношення виду робіт ЩОд;
– коефіцієнт резервування постів для компенсації нерівномірного завантаження;
– число робочих днів на рік;
– число змін протягом доби, виконання робіт з ЩОд;
– тривалість виконання протягом зміни робіт за видами ЩОд, год;
– чисельність робітників, одночасно працюючих на одному посту, чол.;
– коефіцієнт використання робочого часу поста.
Рекомендовані значення показників
,
,
,
наведено в ОНТП 01-91.
Кількість механізованих мийних і сушильних постів визначається за формулою:
, (5.57)
де
– облікова кількість рухомого складу, од.
– коефіцієнт технічної готовності рухомого складу;
– тривалість роботи (приймається рівною тривалості повернення рухомого складу на підприємство);
– коефіцієнт «пікового» повернення рухомого складу (
);
– годинна пропускна здатність мийного обладнання приймається за паспортною характеристикою.
Мінімальну кількість робочих постів з ЩОт слід визначати за формулою:
(5.58)
де
– річний об’єм робіт ЩОт, люд.-год;
Мінімальна кількість постів ТО-1 і ТО-2, загальної і поглибленої діагностики, розбірно-складальних і регулювальних робіт ПР, зварювально-бляхарських, деревообробних і малярних робіт слід визначати за формулою:
(5.59)
де
– річний об’єм робіт, люд.-год;
– коефіцієнт резервування постів;
– число робочих днів на рік;
– число робочих змін на добу;
– тривалість зміни, год;
– чисельність одночасно працюючих на одному посту, чол.;
– коефіцієнт використання робочого часу поста.
При визначенні кількості виробничих постів загальної діагностики слід підсумовувати об’єм контрольно-діагностичних робіт ТО-1 і 50% об’єму контрольно-діагностичних робіт ПР.
При визначенні кількості виробничих постів поглибленої діагностики слід підсумовувати об’єм контрольно-діагностичних робіт ТО-2 і 50% об’єму контрольно-діагностичних робіт ПР.
При розрахунку кількості постів ТО-1 і ТО-2 із загального об’єму робіт слід віднімати об’єм контрольно-діагностичних робіт.
При сумарній розрахунковій кількості постів загальної і поглибленої діагностики рівній або меншій одиниці, ці роботи допускається проводити на одному посту з використанням універсального обладнання і переносних діагностичних приладів.
При розрахунковому коефіцієнті завантаження діагностичних постів різного призначення, рівному або менше 0,75, допускається на цих постах проведення регулювальних робіт.
Перше і друге технічне обслуговування, а також загальна діагностика, можуть проводитися на потокових лініях, індивідуальних проїзних або тупикових спеціалізованих постах.
Допускається на одних і тих самих виробничих постах передбачати виконання ТО-1 і ТО-2 автомобілів або автопоїздів з організацією робіт в різні зміни доби.
При виконанні ТО-1 і ТО-2 в різні зміни доби допускається виконання змащувально-очисних операцій на загальних спеціалізованих виробничих постах.
При розрахунковій кількості робочих постів загальної діагностики, рівній або менше 0,5, допускається розміщувати діагностичне обладнання на потоковій лінії ТО-1.
Поглиблена діагностика автомобілів повинна проводитися на індивідуальних спеціалізованих виробничих постах.
Кількість допоміжних постів контрольно-пропускного пункту визначається за формулою:
(5.60)
де
– облікова кількість рухомого складу, од.;
– коефіцієнт технічної готовності рухомого складу;
– тривалість роботи (приймається рівною тривалості повернення рухомого складу на підприємство);
– коефіцієнт «пікового» повернення рухомого складу
;
– годинна пропускна здатність одного поста.
Розрахунок потокових ліній періодичної дії.
Такі лінії використовуються в основному для ТО-1 і ТО-2. Вихідною величиною, що характеризує потік періодичної дії, є такт лінії. Під тактом лінії розуміють інтервал часу між двома автомобілями, які послідовно сходять з лінії і пройшли даний вид обслуговування:
, (5.61)
де
– трудомісткість робіт з ТО, люд.-год;
– загальне число технологічно необхідних робітників, які працюють на лінії обслуговування;
– час переміщення автомобіля з поста на пост, хв.
Число робітників на лінії обслуговування:
, (5.62)
де
– число постів лінії;
– середнє число робітників на посту лінії обслуговування.
Таким чином,
. (5.63)
Число постів лінії (
) для даного виду обслуговування призначають виходячи зі змісту робіт, їх технологічної послідовності, об’єму робіт і можливої спеціалізації постів за видом робіт. З цією метою необхідно в першу чергу використовувати операційно-технологічні карти, складені по агрегатах і системах, і які вміщують весь перелік операцій за даним видом обслуговування. На основі цих карт орієнтовно групують роботи за наміченим числом постів з урахуванням спеціалізації робіт і необхідністю їх раціоналізації за послідовністю виконання, а також трудомісткістю на постах. При цьому останню необхідно співвідносити з числом виконавців (робочих) на постах, враховуючи необхідність найкращого використання фронту робіт.
Для розрахунку такту лінії при встановленому числі постів середнє число робочих
на посту може бути призначено згідно з рекомендаціями розрахунку кількості постів ТО і ПР. Крім того, при розрахунку
число
може бути призначено не тільки цілим, але і дробовим числом при умові, що добуток
буде виражено цілим числом або дуже близькою до нього величиною. Наприклад, при
і
,
або
і
,
.
Це пояснюється тим, що робочі на лінії обслуговування можуть бути розподілені по постах в кількості, відмінній від середнього і фактично рівного цілого числа, і відповідно об’єма робіт, що виконуються на кожному посту. Але при цьому повинна зберігатися умова рівності такту кожного поста такту лінії. Наприклад, для лінії, яка складається з трьох постів,
, (5.64)
де
,
,
– об’єми робіт, які виконуються на відповідних постах, люд.-год;
,
,
– число робочих на постах.
При використанні конвеєру час переміщення автомобіля з поста на пост дорівнює:
, (5.65)
де
– габаритна довжина автомобіля (автопоїзда), м;
– відстань між автомобілями, які стоять на двох послідовних постах, м;
– швидкість пересування автомобіля конвеєром, м/хв.
Значення
приймають за технічною характеристикою для вибраного типу конвеєра. Для виготовляємих ланцюгових поздовжніх конвеєрів
м/хв. Відстань а відповідно до будівельних норм і правил для підприємств з обслуговування автомобілів (СНиП ІІ-93-74) повинна бути не менше 1,2 м для автомобілів І категорії, 1,5 м – ІІ і ІІІ категорій і 2,0 м – ІV категорії.
Число ліній обслуговування
, (5.66)
де
– час, який необхідно на ТО всіх автомобілів, хв;
– фонд часу одної лінії обслуговування, хв.
Оскільки
, то число ліній обслуговування
, (5.67)
де
– ритм виробництва, тобто час, який в середньому потрібно на випуск автомобіля з даного виду ТО.
Число ліній обслуговування може бути визначено також із можливої пропускної здатності
однієї лінії:
;
. (5.68)
При розрахунку числа ліній необхідно підбирати значення
так, щоб співвідношення
було виражено цілим числом або близьким до нього, але не перевищуючим ціле число ліній, оскільки в протилежному випадку лінія буде перевантаженою. Допустиме відхилення може бути прийняте не більше 0,08 в перерахунку на одну лінію. Якщо при розрахунку число ліній не задовольняє вказані умови, то слід виконати перерахунок такту ліній, змінивши значення
.
При організації процесів обслуговування на потоковій лінії періодичної дії після закінчення робочого дня не повинно залишатися автомобілів. Це обумовлює необхідність ступінчастого приходу робочих на лінію. Пости лінії будуть включатися в роботу послідовно з інтервалом часу, рівним такту лінії. При цьому кожний пост буде працювати протягом часу
, а загальна тривалість роботи лінії збільшується на час
.
При змішаному рухомому складі, який має різну трудомісткість ТО, коли виробнича програма з кожного типу недостатня для організації окремих потокових ліній, обслуговування різних груп рухомого складу можливо проводити і на одній лінії в різні дні тижня або години доби (зміни). При цьому потокова лінія за своєю будовою і обладнанням повинна відповідати вимогам кожного типу рухомого складу.
Виробничі програми з ТО-1 і ТО-2 з часом можуть змінюватись в зв’язку з удосконаленням режиму ТО, зміною типажу і чисельності рухомого складу. Тому при проектуванні підприємств лінії ТО при можливості слід розробляти технологічно і конструктивно так, щоб можливо було проводити ТО-1 і ТО-2 на одній лінії, але в різний час. Крім цього для уніфікації потокових ліній більш раціонально використовувати виробничі площі, обладнання.
Розрахунок потокових ліній неперервної дії.
Такі лінії використовують для виконання прибирально-мийних робіт ЩО з використанням механізованих установок для миття і сушіння (обдування) автомобілів.
При повній механізації робіт з миття і сушіння автомобілів і відсутності прибиральних операцій, які виконуються на інших постах вручну, число постів лінії відповідає числу механізованих установок (для миття автомобілів, дисків коліс, сушіння). Робітники на лінії при цьому можуть бути відсутніми за виключенням оператора для керування установками. Для забезпечення максимальної продуктивності лінії пропускна здатність окремих постових установок повинна бути рівною пропускній здатності основної установки для миття автомобілів. В цьому випадку такт лінії
і необхідна швидкість конвеєра
визначаються з виразу:
;
, (5.69)
де
– продуктивність механізованої мийної установки автомобілів на лінії (для вантажних автомобілів 15-20, легкових – 30-40 і автобусів – 30-50 авт./год);
– габаритна довжина автомобіля (автопоїзда), м;
– відстань між автомобілями на постах лінії, м.
Якщо на лінії обслуговування передбачається механізація тільки мийних робіт, а інші виконуються вручну, то такт лінії (в хвилинах) розраховується з урахуванням швидкості переміщення автомобілів (2-3 м/хв), яка забезпечує можливість виконання робіт вручну в процесі руху автомобіля. В цьому випадку такт лінії
. (5.70)
Пропускна здатність (авт./год) лінії ЩО
. (5.71)
Число постів на лінії ЩО слід призначати за умови їх спеціалізації за видами робіт, наприклад, прибирання, миття, обтирання (обсушування) і т. ін.
Число робочих
, зайнятих на постах ручного оброблення зони ЩО, визначається так:
, (5.72)
де
– число ліній ЩО;
– трудомісткість робіт ЩО, які виконуються вручну, люд.-год.
Розподіл робочих на постах ручного оброблення виконується виходячи з трудомісткості робіт на даному посту і такту лінії.
Слід мати на увазі, що механізація робіт тільки на одному посту лінії обслуговування викликає значне зменшення її такту і, як наслідок, збільшення
на постах ручного оброблення. В результаті механізація робіт тільки на одному посту не дає скорочення робочих, тому необхідно при можливості використовувати механізацію робіт на всіх постах лінії.
Для потоку неперервної дії число ліній
. (5.73)
3. Визначення площ виробничо-складських приміщень, зон зберігання і допоміжних приміщень.
Площі АТП за своїм функціональним призначенням поділяються на три основні групи: виробничо-складські, зберігання рухомого складу та допоміжні.
В склад виробничо-складських приміщень входять зони ТО і ПР, виробничі дільниці ПР, склади, а також приміщення технічних служб і пристроїв (компресорні, трансформаторні, насосні, вентиляційні камери тощо). Для малих АТП при невеликій виробничій програмі деякі дільниці з однорідним характером робіт, а також окремі складські приміщення можуть бути об’єднані.
В склад площ зон зберігання (стоянки) рухомого складу входять площі стоянок (відкритих або закритих) з урахуванням площі, яку займає обладнання для підігріву автомобілів (для відкритих стоянок), рамп і додаткових поверхових проїздів (для закритих багатоповерхових стоянок).
В склад допоміжних площ підприємства відповідно до СНиП ІІ-92-76 входять: санітарно-побутові приміщення, пункти громадського харчування, охорони здоров’я (медичні пункти), культурного обслуговування, управління, приміщення для навчальних занять і громадських організацій.
Розрахунок площ зон ТО і ПР. Залежно від стадії виконання проекту площі зон ТО і ПР розраховуються двома способами:
– за питомими площами – на стадії техніко-економічного обґрунтування та вибору об’ємно-планувального рішення, а також при попередніх розрахунках;
– за графічною побудовою – на стадії розроблення планувальних рішень зон.
Площа зони ТО або ПР визначається за формулою:
, (5.74)
де
– площа, яку займає автомобіль в плані (за габаритними розмірами), м2;
– число постів;
– коефіцієнт щільності розміщення постів.
Коефіцієнт
являє собою відношення площі, яку займають автомобілі, проїзди, проходи, робочі місця, до суми площ проекцій автомобілів в плані. Величина
залежить від габаритів автомобіля і розташування постів. При односторонньому розташуванні постів
. При двосторонньому розташуванні постів і потоковому методі обслуговування
може бути прийнятим рівним 4-5. Менші значення
приймаються для великогабаритного рухомого складу і при числі постів не більше 10.
Розрахунок площ виробничих дільниць
Площі дільниць розраховують за сумарною площею горизонтальної проекції обладнання, і коефіцієнтом щільності його розташування. Площа дільниці визначається за формулою:
, (5.75)
де
– сумарна площа горизонтальної проекції за габаритними розмірами обладнання, м2;
– коефіцієнт щільності розміщення обладнання.
Для розрахунку
попередньо на основі табеля і каталогів технологічного обладнання [41, 42, 44, 45] складається відомість обладнання і визначається його сумарна площа
на дільниці.
Якщо в приміщеннях передбачаються місця для автомобілів або кузовів, то до площі, яку займає обладнання даної дільниці, необхідно додати площу горизонтальної проекції автомобіля або кузова.
Значення коефіцієнта
для відповідних виробничих дільниць (приміщень), наведено в ОНТП 01-91.
В окремих випадках для наближених розрахунків площі дільниць можуть бути визначені за числом працюючих на дільниці в найбільш завантажену зміну (табл. 5.39).
Таблиця 5.39 – Приблизні площі виробничих дільниць ТО і ПР залежно від числа працюючих (за даними Гіпроавтотранса)
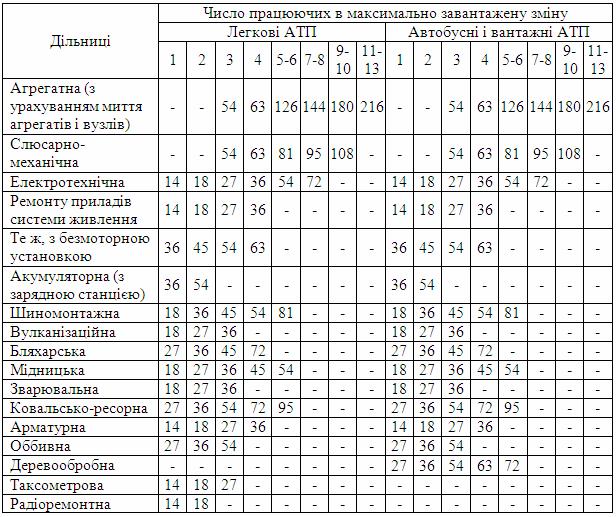
Примітки:
1. При розміщенні на виробничих дільницях імпортного обладнання або високопродуктивного проектного обладнання площа дільниці повинна бути перевірена графічним методом (розташуванням обладнання);
2. При суміщенні в одному приміщенні двох або декількох дільниць площа приймається за сумарним числом працюючих на відповідній дільниці;
3. Площі для виробничих постів в шиномонтажному, бляхарському, зварювальному, оббивному і інших окремих приміщеннях не враховані.
Розрахунок площ складських приміщень
Нормативи площі складських приміщень АТП, експлуатаційних і виробничих філіалів, БЦТО і ВТК, встановлені виходячи з тривалості зберігання матеріалів і запасних частин.
Площі складських приміщень і споруд АТП
визначаються добутком питомих нормативів
на чисельність рухомого складу і на коригуючі коефіцієнти залежно:
– від середньодобового пробігу рухомого складу;
– від чисельності технологічно сумісного рухомого складу;
– від типу рухомого складу;
– від висоти складування;
– від категорій умов експлуатації.
Результуючий коефіцієнт коригування визначається як добуток окремих коефіцієнтів, таким чином площа відповідного складського приміщення визначається за формулою:
, (5.76)
де
– списочна чисельність рухомого складу.
Числові значення нормативів площ та коефіцієнтів коригування наведено в ОНТП 01-91.
Розрахунок площі зони зберігання (стоянки) автомобілів
При укрупнених розрахунках площа зони зберігання визначається за формулою:
, (5.77)
де
– площа, яку займає автомобіль в плані (за габаритними розмірами), м2;
– число автомобіле-місць зберігання;
– коефіцієнт щільності розміщення автомобіле-місць зберігання.
Величина
залежить від способу розміщення місць зберігання і приймається рівною 2,5-3,0.
Залежно від організації зберігання рухомого складу на АТП автомобіле-місця можуть бути закріплені за певними автомобілями або знеособлені.
Число автомобіле-місць зберігання при закріпленні їх за автомобілями відповідає списковому складу парку, тобто
. (5.76)
При знеособленому зберіганні автомобілів число автомобілемісць
, (5.77)
де
– число постів ПР;
– число постів ТО;
– число постів очікування (підбору);
– число автомобілів, які знаходяться в КР;
– середнє число автомобілів, які постійно відсутні на підприємстві (цілодобова робота на лінії, відрядження).
Розрахунок площ допоміжних приміщень
Допоміжні приміщення (адміністративні, суспільні, побутові) є об’єктом архітектурного проектування і повинні відповідати вимогам СНиП ІІ-92-76 «Вспомогательные здания и помещения промышленных предприятий».
На стадії техніко-економічного обґрунтування і попередніх розрахунків орієнтовна загальна площа допоміжних приміщень може бути визначена за графіком, наведеним на рис. 5.8.
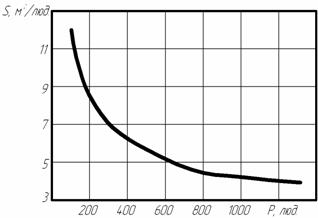
Рисунок 5.8 – Залежність питомої площі S допоміжних приміщень
від числа працюючих Р
Детальне розроблення допоміжних приміщень виконується в об’ємі архітектурно-будівельної частини проекту на основі завдань проектувальників-технологів. Розрахунок площ окремих допоміжних приміщень виконується за відповідними нормами і числом працюючих.
Площі адміністративних приміщень розраховуються виходячи зі штату управлінського апарату, а суспільних приміщень – спискового числа працюючих. Площі побутових приміщень розраховуються виходячи з штатної кількості працюючих, числа працюючих в найбільш багаточисельній зміні, групи виробничого процесу за класифікацією СНиП ІІ-92-76,
співвідношення числа чоловіків і жінок.
Площі технічних приміщень компресорної, трансформаторної і насосної станції, вентиляційних камер і інших приміщень розраховуються в кожному окремому випадку за відповідними нормативами залежно від прийнятої системи і обладнання електропостачання, опалення, вентиляції і водопостачання.
В пункті 2.1.4 виконується технологічне планування підприємства, яке включає розроблення загального технологічного процесу ТО та ремонту автомобілів та об’ємно-планувальних рішень генерального плану та виробничого корпусу АТП.
1. Розроблення схеми організації ТО і ПР автомобілів і графіка виробничого процесу АТП.
Технологічною основою планувального рішення є функціональна схема (рис. 5.9) і графік виробничого процесу (рис. 5.10).
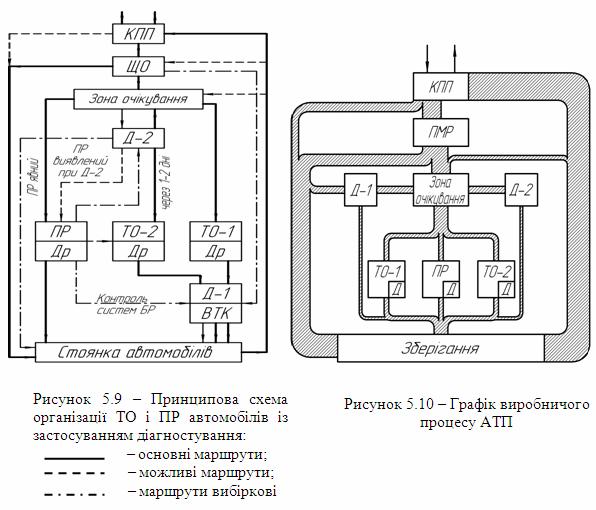
Функціональна схема комплексного АТП визначає закономірність проходження автомобілем окремих етапів його технічної підготовки. Відповідно до цього функціональна схема зумовлює послідовність і незалежність розташування в просторі виробничих зон і відділень підприємства. Проте вона не фіксує потоків руху рухомого складу (кількісну характеристику процесу), який проходить ці етапи. Тому, крім схеми, потрібний графік виробничого процесу, який будують у відповідному масштабі за даними розрахунку програми ремонтно-обслуговуючого виробництва АТП. Графік є основою для вибору розташування зон підприємства. Він може змінюватись залежно від нормативів, покладених в основу технологічного розрахунку. На цю обставину при проектуванні треба звертати особливу увагу. Раціональне планування підприємства має забезпечувати безперешкодне і незалежне проходження автомобілем будь-якого самостійного маршруту.
2. Розроблення генерального плану підприємства.
На генеральному плані показують будівлі і споруди за їхніми габаритними обрисами, розміщенням, площадки для відкритого зберігання автомобільної техніки, основні і допоміжні шляхи руху рухомого складу на території АТП. Технологічною основою генерального плану є функціональна схема і графік виробничого процесу.
На стадії техніко-економічного обґрунтування та за попередніми розрахунками необхідна площа ділянки підприємства (в гектарах) визначається за формулою:
, (5.78)
де
– площа забудови виробничо-складських будівель, м2;
– площа забудови допоміжних будівель, м2;
– площа відкритих площадок для зберігання рухомого складу, м2;
– щільність забудови території, %.
Щільність забудови підприємства визначається відношенням площі забудови до площі ділянки підприємства. В табл. 5.40 дана мінімальна щільність забудови (в відсотках) підприємств автомобільного транспорту відповідно до вимог СНиП ІІ-89-80.
Вказану щільність забудови допускається знижувати, але не більше ніж на 10% при наявності відповідного техніко-економічного обґрунтування, в тому числі при розширенні та реконструкції підприємства.
Розробляючи генеральний план, враховують загальні і місцеві вимоги. Загальні вимоги диктуються призначенням АТП та його виробничими процесами, складом і взаємозв'язком будівель і споруд, черговістю будівництва і перспективами розширення, нормативними вимогами до організації і забудови території. Місцеві вимоги зумовлюються розташуванням земельної ділянки в плані району будівництва і щодо проїздів спільного користування; розмірами, конфігурацією, рельєфом і гідрологічною характеристикою ділянки; характером забудови сусідніх ділянок; містобудівними й архітектурними вимогами і т. ін.
Таблиця 5.40 – Мінімальна щільність забудови АТП
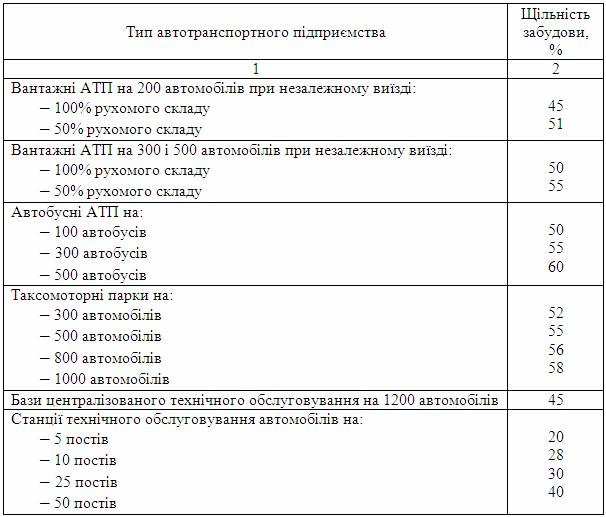
Розрізняють два способи забудови земельної ділянки: блокований (усі основні функції підприємства виконують в одній спільній будівлі) і павільйонний (усі основні функції підприємства виконуються в окремих будівлях). Для вибору способу забудови обов’язково виконують попереднє детальне техніко-економічне обґрунтування.
Перевагу віддають блокованій забудові. Вона дає змогу знизити вартість будівництва й експлуатації будівель на 15...20% порівняно з павільйонною, поліпшити виробничі зв’язки між зонами й відділеннями, зменшити площу земельної ділянки.
Павільйонна забудова дає змогу спростити організацію і прискорити будівництво, вводити об’єкти в дію поетапно, поліпшити природне освітлення і вентиляцію приміщень та ін. Проте через істотні недоліки (збільшення площі земельної ділянки, загальне подорожчання будівництва й експлуатації будівель, зниження рівня архітектурного оформлення району) павільйонна забудова має обмежене застосування. Її можна рекомендувати при проектуванні підприємств для обслуговування великогабаритного рухомого складу з метою максимального скорочення його маневрування всередині будівлі; при будівництві підприємства на горбкуватій, гірській місцевості або в районі з м’яким кліматом; у разі реконструкції підприємства та наявності великої вільної території; при потребі стадійного розвитку підприємства, зумовленого поступовим фінансуванням. Мийну для рухомого складу дозволяється розміщувати в окремих будівлях.
Будівлі можуть бути одно-, багато- і різноповерховими (змішаної поверховості). Технологічно одноповерхова забудова доцільніша. Тому в усіх випадках, коли площа земельної ділянки достатня і немає вказівок щодо поверховості містобудівних та архітектурних органів, треба будувати одноповерхові приміщення. При багатоповерховій забудові на першому поверсі розміщують виробничі зони, а на решті – зону зберігання.
Розробляючи генеральний план, велику увагу звертають на відстані між будівлями, що враховують санітарні, будівельні і протипожежні норми. Мінімальні відстані між будівлями всередині підприємства становлять 12 м. Якщо в одній із будівель розміщений склад пального і мастильних матеріалів, то відстані збільшують у два рази. Відстань від зони зберігання автомобілів (відкритої) до зони ТО або ремонту повинна бути 10 м, між сусідніми підприємствами промислового типу – 20 м, до огорожі (паркану) або глухої вогнестійкої стіни – 2 м.
Важливим елементом генерального плану є проїзди. Вони повинні мати тверде покриття і поздовжні ухили більше як 4%. Ширина проїздів 3 м при односторонньому і 6 м при двосторонньому русі. Відстань між проїздом і будівлею завдовжки понад 20 м становить 3 м, в усіх інших випадках – 1,5 м.
Рух автомобілів на території АТП звичайно організовують кільцевим одностороннім способом. Якщо такий спосіб важко застосувати, то передбачають у тупиковому проїзді двостороннього руху майданчик розвороту рухомого складу на 180°. В усіх випадках організації руху на території АТП треба намагатись скоротити шлях автомобілів, не допускаючи зустрічного руху на одній смузі і пересічення потоків.
У зоні зберігання автомобілі розміщують групами (в групі не більше як 200 одиниць). За правилами протипожежної безпеки відстань між групами повинна бути не менше як 20 м.
В’їзд автомобілів на територію АТП і виїзд із неї здійснюється через ворота; для великих АТП – двоє робочих і двоє запасних воріт, для середніх АТП – одні робочі ворота. Робочі ворота розміщують від червоної лінії (внутрішньої лінії тротуару) на відстані не менше ніж довжина найбільшого автомобіля в цьому АТП. Ворота в’їзду повинні бути розміщені раніше, ніж ворота виїзду, за ходом дорожнього руху. Це забезпечує на території АТП правосторонній рух переважно проти годинникової стрілки і виключає пересічення шляхів.
Робочі ворота, як правило, використовують для постійного в’їзду рухомого складу, тому їх розміщують із боку вулиці або проїзду з мало-інтенсивним рухом транспорту. Біля робочих воріт розміщують контрольно-пропускний пункт. Робочі ворота звичайно роблять роздільними: одні для в’їзду, другі для виїзду. Мінімальні розміри воріт при одноповерховому зберіганні автомобілів 3,5 ? 3,5 м, а при багатоповерховому – 3,5 ? 4,2 м.
Територію земельної ділянки, вільну від забудови, проїздів і зон зберігання, впорядковують й озеленюють. Біля АТП для стоянки автомобілів індивідуальних власників обладнують спеціальну площадку. На території АТП можуть бути розташовані приміщення для ТО, ремонту і зберігання рухомого складу: адміністративно-громадські, санітарно-побутові та різні допоміжні приміщення.
При розробленні генерального плану необхідно передбачити благоустрій території підприємства, спорудження спортивних площадок, озеленення. Площа озеленення повинна складати не менше 15% площі підприємства при щільності забудови менше 50% та не менше 10% при щільності більше 50%.
Основними показниками генерального плану є площа та щільність забудови, коефіцієнт використання і озеленення території.
Площа забудови визначається як сума площ, зайнятих будівлями та спорудами всіх видів, включаючи навіси, відкриті стоянки автомобілів і склади, резервні дільниці, намічені відповідно до завдання на проектування. В площу забудови не включають площі, зайняті брукуваннями, тротуарами, автомобільними дорогами, відкритими спортивними площадками, площадками для відпочинку, зеленими насадженнями, відкритими стоянками автомобілів індивідуального користування.
Коефіцієнт використання території визначається відношенням площі, зайнятої будівлями, спорудами, відкритими площадками, автомобільними дорогами, тротуарами і озелененням, до загальної площі підприємства.
Коефіцієнт озеленення визначається відношенням площі зелених насаджень до загальної площі підприємства.
При розробленні генеральних планів підприємств необхідно користуватися таким.
1. На території підприємства перед в’їздом на пости прибиральних, мийних і інших робіт комплексу ЩО слід передбачати майданчики накопичення рухомого складу місткістю не менше 10-ти відсотків пропускної спроможності відповідних постів.
2. На території промислових філій АТП, ЦСП, БЦТО, ВТК, СТОА і ВАСНУВ слід передбачати майданчики для тимчасового зберігання рухомого складу, який належить іншим підприємствам, підрозділам підприємств й громадянам і прибуває для виробництва робіт ТО і ПР; місткість вказаних майданчиків повинна встановлюватися технологічною частиною проекту.
3. Розставлення рухомого складу на відкритому майданчику, розташованому на території підприємства, слід передбачати відповідно до схем, вказаних на рис. 5.11.
Розставлення за схемами 1-4 призначене для зберігання рухомого складу без пристрою підігріву автомобілів, а за схемами 5-7 – з пристроєм підігріву автомобілів для забезпечення запуску двигунів в холодну пору року.
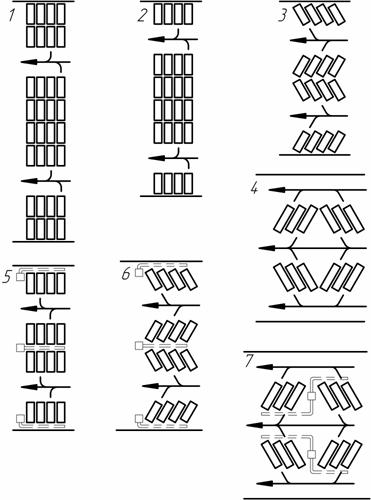
Рисунок 5.11 – Схеми розставлення рухомого складу на відкритому
майданчику, розташованому на території підприємства
Розставлення за схемами 1, 2 і 5 призначене для зберігання одиночних автомобілів і автобусів; за схемами 3 і 8 – для автопоїздів у складі сидільного тягача з напівпричепом і зчленованих автобусів; за схемами 4 і 7 – для автопоїздів у складі автомобіля з одним або декількома причепами.
Розставлення на відкритому майданчику легкових автомобілів, які належних громадянам, слід передбачати за схемами 3 і 5 без пристрою підігріву.
При розміщенні рухомого складу на відкритому майданчику рекомендується приймати кут між повздовжньою віссю автомобіля і віссю внутрішнього проїзду:
– для одиночних автомобілів і автобусів – 90°;
– для автопоїздів і зчленованих автобусів – від 60° до 45°.
4. Стаціонарні паливозаправні пункти (СПЗП) і спеціальні майданчики для розміщення пересувних автозаправних станцій на шасі автомобіля або причепа (ПАЗС) слід передбачати на території підприємства за умови забезпечення зберігання і роздавання не менше трьох сортів палива для АТП вантажних автомобілів і автобусів і двох сортів палива для АТП легкових автомобілів. Запас зберігаємого палива приймається не менше 5 днів.
Загальна місткість паливних резервуарів не повинна перевищувати:
– для стаціонарних ПЗП – 300 м3;
– для пересувних ПАЗС – 30 м3.
Кількість паливороздавальних колонок у випадку, не обумовленому завданням на проектування, слід приймати з розрахунку:
– 1 колонка на 100 автобусів;
– 1 колонка на 150 вантажних автомобілів;
– 1 колонка на 200 легкових автомобілів.
ПАЗС рекомендується застосовувати в АТП при чисельності автомобілів не більше 200 од.
Відстань від майданчика для пересувних ПАЗС до будівель і споруд АТП слід передбачати відповідно до ВСН-01-89 Мінавтотрансу РСФСР як для майданчиків з автомобілями, що перевозять ПММ, до будівель і споруд сусідніх промпідприємств – не менше 40 м.
Майданчики СПЗП і для ПАЗС повинні розташовуватися, як правило, в підвітряній зоні вітрів переважаючого напряму відносно адміністративно-побутового корпусу АТП, бути сприятливими для озеленення, при цьому насадження не повинні погіршувати умов видимості і провітрювання.
Схему руху автотранспорту на майданчиках СПЗП і ПАЗС слід приймати односторонньою, з роздільними одна від одної під’їзними дорогами.
Розміри і розміщення майданчиків для СПЗП і ПАЗС повинні забезпечувати незалежний від заправних острівців проїзд автомобілів на стоянку і при виїзді на лінію.
На СПЗП можлива організація маслорозподільного пункту у випадку, обумовленому завданням на проектування.
5. Вимоги до розміщення на території підприємства будівель і споруд, а також до санітарно-захисної зони слід приймати за ВСН-01-89 Мінавтотрансу РСФСР.
Споруди і приміщення для зберігання автомобілів
6. Зберігання рухомого складу в АТП може здійснюватися на відкритому майданчику, під навісом або в закритому приміщенні.
Способи зберігання рухомого складу в автотранспортних підприємствах слід приймати, як правило, залежно від типу автомобілів, кліматичних умов і видів транспортної роботи, наведених в таблиці 5.41.
Таблиця 5.41 – Способи зберігання рухомого складу
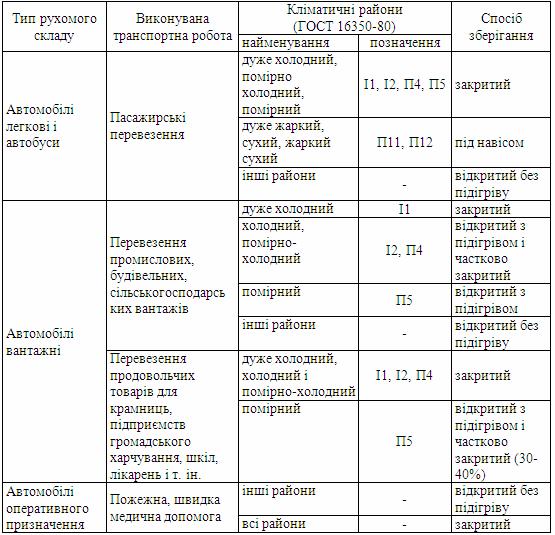
Зберігання легкових автомобілів на СТОА слід передбачати залежно від кліматичних умов:
– закрите для дуже холодного кліматичного району (І1);
– під навісом для дуже жаркого сухого кліматичного району (П12);
6.1. Розставлення рухомого складу в приміщеннях стоянки слід передбачати відповідно до схем, вказаних на рис. 5.12.
Схеми 1-9 призначені для зберігання одиночних автомобілів і автобусів, схеми 10 і 11 – для автопоїздів і зчленованих автобусів.
Кількість автопоїздів і зчленованих автобусів у напрямі руху при розставленні за схемами 10 і 11 не повинна перевищувати восьми.
При розставленні автомобілів різних категорій допускається розміщення автомобілів меншої довжини за схемами 3 і 6 в три ряди і за схемами 10 і 11 в десять рядів у напрямі руху.
Схеми 1, 2 і 4 призначені для зберігання автомобілів, які постійно повинні бути готові до виїзду, і легкових автомобілів, які належать громадянам.
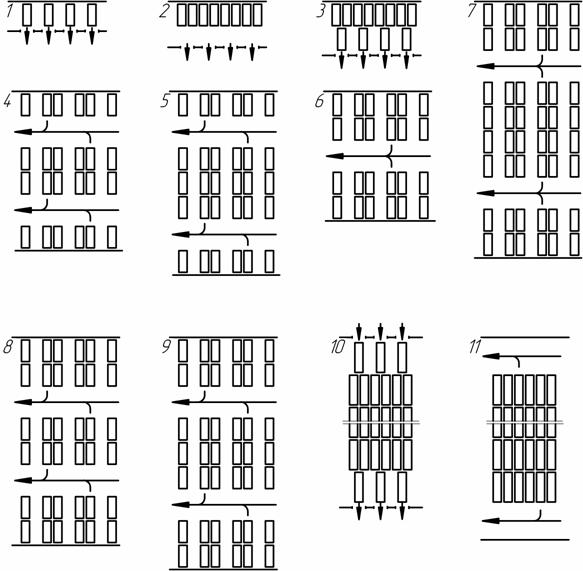
Рисунок 5.12 – Схеми розставлення рухомого складу в приміщеннях стоянки
3. Розробка плану виробничого корпусу.
Вибір оптимального об’ємно-планувального рішення конструктивної схеми будівлі має велике значення при проектуванні АТП. Розміри кроку колон і прольотів, корисну висоту поверхів вибирають так, щоб забезпечити раціональне використання корисної площі будівлі, створити найкращі умови для маневрування автомобілів. Треба також враховувати перспективні можливості використання будівлі (реконструкцію).
Конструктивну схему будівлі вибирають так, щоб вона могла забезпечити застосування прогресивних уніфікованих конструкцій, які відповідають економічним вимогам. Широко використовують уніфіковані типові секції, прольоти, конструкції і деталі. Взаємоув’язувати розміри будівель та окремих їхніх елементів дає змогу прийнята єдина модульна система (ЄМС). Вона лежить в основі уніфікації і типізації об’ємно-планувальних та конструктивних рішень будівель.
Приміщення АТП складаються немов із прямокутних паралелепіпедів, бічні вертикальні ребра яких для міцності виконують у вигляді колон прямокутного, круглого або кільцевого перерізів. Найпоширеніші прямокутні колони з розмірами 400 ? 400; 400 ? 600; 400 ? 800; 500 ? 800; 500 ? 500; 500 ? 600 мм та інші.
Центрифуговані колони кільцевого перерізу порівняно з прямокутними дають змогу економити будівельні матеріали (бетону 30...50%, сталі 15...60%), мають гарний зовнішній вигляд, поліпшують видимість і тим самим підвищують безпеку руху.
На кожну пару колон зверху по довжині укладають балки перекриття, що є опорою для кількох плит, які перекривають по ширині верхній простір між балками. Обмежений у плані по кутах чотирма колонами прямокутник утворює так звану сітку колон. У будівельній документації сітку колон умовно позначають цифровим добутком кроку колон на прогін (наприклад, 6 ? 12; 12 ? 18; 12 ? 24 м). Найменші відстані між осями рядів колон називають кроком колон, а найбільші – прогоном.
Для одноповерхових будівель АТП застосовують багатопрогінні виробничі приміщення, основні несучі конструкції яких – поперечні рами з уніфікованих елементів залізобетонних конструкцій. Сітку колон звичайно беруть 12 ? 18, 12 ? 24, 12 ? 30 м. Висота від підлоги до низу виступаючих конструкцій 4,8...7,2 м. Поперечні рами утворюються з фундаментів стаканного типу, колон прямокутного перерізу і несучих конструкцій покриттів із попередньо напруженого залізобетону. Уздовж будівель по несучих конструкціях установлюють ребристі плити з розмірами 3 ? 12 м.
Зверху для перекриття приміщень використовують будівельні балки (або ферми), панелі, плити і т.д. Будівельні балки (залізобетонні) застосовують при прогонах до 24 м, а ферми (сегментні, трапецієвидні або з паралельними поясами) – при прогонах 24 м і більше. Металевими фермами перекривають великі прогони.
Є проекти одноповерхових будівель АТП з укрупненою сіткою колон (40 ? 40 м і більше) або взагалі без них. Для покриття таких будівель застосовують сферичні оболонки подвійної кривизни, циліндричні оболонки, хвилясті склепіння, висячі вантові системи, які дають змогу збільшити прогони до 80...100 м і більше. Це дає змогу цілком виключити колони в зонах інтенсивного маневрування автомобілів, споруджувати будівлі не тільки прямокутного, а й круглого перерізу.
У великих зонах зберігання і ТО автомобілів часто для поліпшення проїзду автомобілів прибирають по всій довжині прогонів один ряд колон. Замість них накладають підкроквяні балки або ферми, на які вкладають звичайні кроквяні балки завдовжки 12, 18 і 24 м. Балки тут опираються не на колони, а на підкроквяні конструкції.
Одноповерхові будівлі АТП іноді покривають легкими тентовими або пластмасовими навісами.
Поряд з перевагами уніфікованого будівництва застосування єдиної стандартної сітки колон не завжди забезпечує раціональне планування виробничих приміщень АТП, оскільки різні групи приміщень висувають різні вимоги до сітки колон. Так, для приміщень постів ТО і ПР доцільно мати вільний простір для маневрування автомобілів, що можна забезпечити застосуванням великорозмірної сітки колон. Для виробничих цехів і дільниць доцільно застосовування дрібнорозмірної сітки колон, яка дасть змогу забезпечити раціональне планування приміщень особливо при їх невеликих площах. Крім того, в зонах ТО і ПР, особливо там де використовуються підйомні засоби, необхідна значно більша висота приміщень, ніж на виробничих дільницях.
Таким чином, вказані групи приміщень висувають різні вимоги до сітки колон і висоти приміщень. При цьому об’ємно-планувальне рішення, яке задовольняє одну групу приміщень (пости ТО і ПР), не прийнятно для іншої (цехи і дільниці) і навпаки. Тому в ряді випадків доцільно застосовувати змішану сітку колон, при якій прогони колон вибирають різними для частин будівлі, де буде розміщено зони ТО і ПР та виробничі цехи (дільниці). Наприклад, (6 + 12 + 6) ? 6; (6 + 24) ? 12 м і т. ін.
Конструктивну схему багатоповерхових будівель АТП вибрати значно складніше, ніж одноповерхових. Тут вирішальне значення мають розміри сітки колон. Ідеальною для багатоповерхових будівель АТП є однопрогінна схема без проміжних внутрішніх опор. Оптимальна шири на прогону для таксомоторних АТП – близько 15...18 м. Разом із тим для промислового будівництва розроблено багатоповерхові каркасні будівлі з найпоширенішою сіткою колон 6 ? 6 і 6 ? 9 м. Тому доводиться або використовувати типові рішення з деяким погіршенням експлуатаційних показників, або розробляти різні спеціальні конструктивні схеми для будівель АТП.
Зважаючи на це, сітку колон багатоповерхових будівель звичайно вибирають із різним кроком для кожного напряму. У поперечному напрямі найбільший розмір кроку визначається шириною проїзду, а в поздовжньому – можливістю встановлення автомобілів (звичайно від 2 до 4) між колонами. Наприклад, для легкових автомобілів, крім застосовуваної в промисловому будівництві сітки колон 6 ? 9, використовують 7,5 ? 9; 15,3 ? 6; (9 + 6 + 9) ? 5,5; (6 + 7 + 6) ? 9; (4,5 + 9 + 4,5) ? 7,5; (3+9+3) ? 7,5 м та інші. Висота поверхів 2,8...3,3 м при мінімальній висоті 2,1 м між підлогою і низом виступаючих конструкцій. Для вантажних автомобілів середньої вантажопідйомності розроблено багатоповерховий гараж із сіткою колон 15 ? 10 м.
Окремі приміщення ізолюють одне від одного і від зовнішнього середовища стінами або перегородками. Вибір конструкції стін залежить від призначення або розташування (надземна чи підземна) будівлі, а також від району будівництва. У будівлях, призначених для ТО і ремонту автомобілів, як захисні конструкції застосовують одно- або багатошарові стінові панелі, які забезпечують потрібний волого-температурний режим у приміщеннях. Для підземних будівель, які споруджують відкритим способом, стіни звичайно виконують із збірних залізобетонних плит суцільного або ребристого перерізу у вигляді 2Т різної товщини (залежно від глибини закладання).
При незначній висоті будівлі (2...3 поверхи) стінові панелі можуть бути заввишки на всю будівлю.
Деякі будівлі АТП будують із капітальними стінами, особливо в тих районах де є достатня кількість цегли. Капітальні стіни несучі. Вони сприймають вертикальні навантаження, їх застосовують у будівлях безкаркасних і з наземним каркасом. Капітальні стіни будують із цегли і блоків завтовшки 380, 510, 610 мм. Їх використовують як зовнішні, а також для ізоляції окремих зон і вогненебезпечних приміщень. Колон у капітальних стінах немає.
У каркасних будівлях вертикальне навантаження сприймають колони. Перегородка і несучі стіни виконують захисні функції, їх будують із цегли, дрібних блоків (при товщині стін 120, 250, 380 мм) або зі стінових панелей завтовшки 100, 120, 300 мм (для стін неопалюваних будівель) і 280...300 мм (для опалюваних будівель). Для південних районів несучі стіни використовують як зовнішні стіни. Усередині будівель, крім роздільних перегородок, для часткової ізоляції окремих приміщень (складу, інструментальної і т. ін.) використовують не на всю висоту приміщення дерев’яні або металеві сітки і залізобетонні збірно-розбірні плити заввишки від 2,2 до 3 м.
При будівництві й експлуатації будівлі велику увагу приділяють прорізам (ворота, двері, вікна, ліхтарі та ін.). Ворота розміщують як у зовнішніх стінах, так і в роздільних перегородках, їх використовують для проїзду автомобілів. За конструкцією розрізняють ворота двостулкові, розпашні, розсувні, підйомні і відкатні. Полотна розпашних воріт відчиняються назовні (за вимогами техніки безпеки). Останнім часом широко застосовують хитні ворота, виконані з гуми або прозорого пружного пластику. Такі ворота усувають потребу зупинки транспорту при заїзді в будівлю, оскільки м’який матеріал воріт не завдає пошкоджень автомобілю; зменшуються при цьому і теплові втрати. Звичайно ворота розміщують у торцевих стінах будівель і обладнують повітряно-тепловими завісами з автоматичною дією. Розміри воріт за шириною кратні 500 мм, за висотою – 600 мм, мінімальні розміри 3000 ? 3000 мм.
Для проходу людей в адміністративно-побутових приміщеннях і цехах, де немає великогабаритного устаткування, застосовують одностулкові двері завширшки 750 або 1000 мм. Двостулкові двері використовують у складських приміщеннях і в усіх інших цехах. Ширина цих дверей 1500 або 2000 мм. Стандартна висота усіх дверей 2400 мм.
Виробничі приміщення в денну пору освітлюються природним світлом через вікна в зовнішніх стінах або світлові ліхтарі, влаштовані на дахах будівель у спеціальних прорізах (верхнє освітлення). Окремі широкі приміщення освітлюють штучним світлом. У стінах будівель світлові прорізи роблять у вигляді окремих вікон, стрічкових і суцільних стін. По периметру будівлі вікна розміщують симетрично. Простінки між вікнами мають однакові розміри. Рами вікон роблять одинарними або подвійними залежно від призначення приміщення та кліматичних особливостей району розташування АТП. Широко застосовують економічні спарені віконні рами й одинарні віконні рами з подвійним заскленням. Висота вікон 1,2; 1,8; 2,4 м (кратна 0,6 м), ширина 1,5; 2; 3; 4 м.
Дуже важливим елементом виробничих приміщень є підлога різних видів залежно від призначення приміщення. Наприклад, у зонах зберігання, ТО, у складах запасних частин і агрегатів, у карбюраторному, агрегатному цехах застосовують асфальтобетонну, а в слюсарно-механічному, електротехнічному – торцеву з дерев’яних шашок. Останнім часом підлогу роблять із полімерних матеріалів.
Для з’єднання між поверхами у багатоповерхових будівлях застосовують різні сходи, ліфти і рампи. Прямі рампи роблять аналогічно конструкції міжповерхового перекриття, прийнятої для цієї будівлі. При збірних перекриттях пряма рампа звичайно складається з ребристих плит, укладених на похилі балки. Спіральні рампи виконують монолітними або збірними. Збірні складаються з трапецієвидних або прямо кут-них у плані плит. Є й інші конструкції.
Ширина проїзної частини одноколійних прямолінійних рамп для автомобілів І категорії (довжина до 6 м, ширина до 2,1 м) повинна дорівнювати найбільшій ширині автомобіля плюс 0,8 м; для автомобілів з великими габаритними розмірами – ширині автомобіля плюс 1,2 м; але не менше як 3,5 м. Ширина криволінійних рамп дорівнює ширині смуги, що утворюється в горизонтальній проекції автомобілем І категорії, який рухається, плюс 1 м, а більшого автомобіля плюс 1,5 м, але не менше як 2,5 м.
В загальному планувальному рішенні можливі різні варіанти розташування постів ТО і ПР, а також приміщень виробничих дільниць (рис. 5.13). Розташування виробничих дільниць і складів визначається їх технологічним до основних зон ТО і ПР.
Взаємне розташування виробничих приміщень у плані виробничого корпусу залежить від призначення, виробничих зв'язків, технологічної однорідності виконуваних у них робіт і спільності технічних, будівельних, економічних, санітарно-гігієнічних і протипожежних вимог.
1. Зони ТО-1 і ТО-2 з організацією роботи на потоці розміщують у крайніх частинах будівлі, уздовж або впоперек її осі. Якщо в цих зонах передбачено обслуговування на окремо розташованих постах одиничним методом, то кращим варіантом є розміщення зон у середній частині будівлі, поблизу допоміжних відділень.
2. Розташування зони ЩО залежить від кліматичних умов місцевості, в якій створюється АТП. У південних і центральних районах її створюють в окремому павільйоні. Це сприяє зниженню вологості повітря в основному виробничому корпусі.
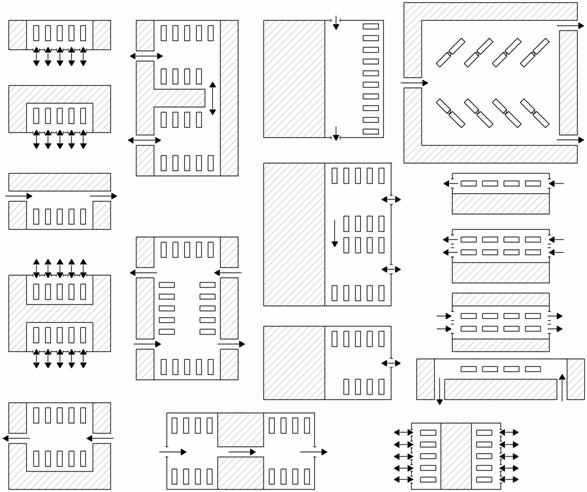
Рисунок 5.13 – Варіанти розташування постів і виробничих приміщень
(останні заштриховані)
3. Зону поточного ремонту розміщують усередині будівлі або уздовж одного з її боків, поблизу відділень, які забезпечують ритмічність роботи постів поточного ремонту.
4. Відділення ремонту й обслуговування агрегатів (механізмів) звичайно розміщують по периметру виробничого корпусу, навколо зон ТО-2 і поточного ремонту з окремо розташованими постами універсального або спеціалізованого типу.
5. Гарячі відділення (ковальське, зварювальне, мідницьке, шиноремонтне) влаштовують в одному блоці (суміжно) і відокремлюють вогнестійкими перегородками від решти приміщень.
6. Групу кузовних відділень (столярне, оббивальне, бляхарське, малярне) з технологічних міркувань розташовують поряд.
7. Механічне, агрегатне, моторне й заготівельне відділення розташовують поблизу зони поточного ремонту і складу агрегатів та запасних частин. Тут же, неподалік від цих відділень, міститься інструментальна комора.
8. Вибираючи місце для постів зон ТО-2 і поточного ремонту відносно вікон, перевагу віддають першим, оскільки на них виконується більше таких операцій, при яких потрібне природне освітлення.
9. Виробничі відділення, що мають технологічний зв’язок із зоною ТО-2 (карбюраторне, акумуляторне, електротехнічне та ін.), розміщують біля цієї зони.
10. Якщо в зоні ТО-2 застосовується потокова лінія з поперечним розташуванням постів, то паралельно цій лінії (проти кожного поста) розміщують пости поточного ремонту. У разі виявлення в процесі профілактики великих несправностей при такому плануванні легко перемістити автомобіль із лінії обслуговування в зону поточного ремонту.
11. При агрегатно-дільничній формі організації виробництва з метою полегшення управління виробничими дільницями відділення і пости цієї дільниці розміщують нерозрізнено.
12. Маслогосподарство з метою скорочення довжини трубопроводів розташовують поблизу постів мащення. Якщо ТО-1 виконується на потоці, то маслогосподарство розміщують біля останнього поста лінії.
13. Компресорну станцію розташовують поблизу тих відділень і зон, у яких стиснуте повітря використовується у найбільших кількостях.
14. Виконуючи планування, не слід приймати таких рішень, при яких потрапити в те чи інше відділення можна тільки через інше. Це порушує зручність роботи і відвертає виконавців. Треба також передбачити можливість транспортування агрегатів з одного приміщення в інше.
15. Усі робочі пости розташовують усередині закритих опалюваних будівель (за винятком постів щоденного обслуговування в районах із теплою зимою).
16. Перед робочими постами залишають простір, достатній для маневрування автомобілів, підвезення спорядження та устаткування, дрібних допоміжних робіт і т. ін.
Залежно від прийнятої форми організаційної побудови технологічного процесу ТО і ремонту автомобілів робочі пости розташовують тупиковим або прямоточним способом. При тупиковому розташуванні постів найпоширеніше прямокутне однорядне розставлення автомобілів. Косокутне розташування постів – під кутом 75, 60, 45 і 30° до осі проїзду – застосовують, коли АТП експлуатує великі автомобілі або для будівництва виділені ділянки видовженої форми. Косокутне розташування постів зменшує корисну площу виробничої зони.
Відстань між робочими постами або автомобілями, встановленими на них, і від елементів будівлі залежно від категорії автомобіля вказана у ОНТП 01-91.
З однієї зони в іншу автомобілі переміщуються проїздами, які можуть проходити всередині будівлі (для районів із холодним кліматом та для малогабаритних автомобілів) або із зовні по території АТП (у південних районах, при експлуатації автопоїздів і великих автомобілів). Внутрішні проїзди збільшують площу будівлі, проте зменшують протяги, втрати теплоти в холодну пору. Зовнішні проїзди зменшують розміри зон, підвищують безпеку руху й поліпшують санітарно-гігієнічні умови праці виконавців робіт при загальному здешевленні будівництва.
Розміри і конфігурація основних зон залежать від кількості і типу робочих постів та потокових ліній. Площі виробничих приміщень при плануванні можуть відхилятись від розрахункових у межах ± 20% (для приміщень, площа яких менша від 100 м2) і ± 10% (для приміщень, площа яких більша від 100 м2).
Місця зберігання автомобілів не повинні з’єднуватися (тобто мати двері або ворота) з приміщеннями, в яких працюють з відкритим вогнем (наприклад, з ковальським, мідницьким, зварювальним), зберігаються горючі і легкозаймисті матеріали (склади масел, оббивальне відділення та ін.) або виділяються вибухонебезпечні і шкідливі гази (акумуляторна, малярне відділення та ін.).
Зони ТО, ПР і зберігання автомобільної техніки повинні мати безпосередній вихід назовні. У приміщеннях, де зберігають до 25 автомобілів або де є до 10 робочих постів (пости потокових ліній за винятком щоденного обслуговування враховують нарівні з одиночними постами), досить одних зовнішніх воріт; до 100 автомобілів на зберіганні або 11...25 робочих постів – не менше двох воріт; 26...50 робочих постів – не менше трьох воріт. Коли є можливість виїзду через суміжні приміщення, кількість воріт може бути скорочена.
При зберіганні більше як 1000 автомобілів на кожні наступні 100 машин добавляють одні ворота.
Безпосередній вихід назовні мають також деякі виробничі і складські приміщення: склад легкозаймистих матеріалів, малярне відділення, приміщення для ацетиленогазозварювальних робіт і регенерації масел, насосна для перекачування масел незалежно від площі, яку вона займає; зарядне відділення акумуляторного цеху при площі більше як 25 м2; склад масел і обтиральних матеріалів при площі понад 50 м2; зварювальне, ковальсько-ресорне, термічне й вулканізаційне відділення при площі понад 100 м2.
Деякі зони і цехи за санітарно-гігієнічними вимогами ізолюють і розташовують осторонь від основних приміщень. Наприклад, через підвищену вологість повітря щоденне обслуговування виділяють у самостійне приміщення. Малярний цех (дільницю) розміщують осторонь і з окремим виїздом. Ізолюють від інших приміщень також зарядне відділення акумуляторного цеху, газозварювальне відділення та ін.
Приміщення, які повинні мати природне освітлення, розташовують по зовнішньому периметру будівлі. Внутрішні площі будівлі відводять під другорядні приміщення, зону зберігання автомобілів, склади, побутові кімнати, коридори і т. д.
За санітарними нормами заборонено будувати приміщення площею менш як 10 м2 і з довжиною стіни менше як 3 м. Дозволено суміщати для невеликих АТП і СТО виконання в одному приміщенні таких робіт: постові роботи на ТО і ПР; постові роботи на поточному ремонті з агрегатними й шиномонтажними; агрегатні, слюсарно-механічні; електротехнічні і карбюраторні; ковальсько-ресорні, зварювальні, мідницькі, бляхарські і термічні; столярні, оббивальні, кузовні, бляхарські (без застосування вогню).
У разі неможливості розміщення усіх виробничо-підготовчих приміщень на першому поверсі їх розміщують на поверхах, що розташовані вище, або на антресолях, у першу чергу – приміщення для електротехнічних, карбюраторних і оббивних робіт, у другу чергу – для механічних і агрегатних робіт і частково для складу запасних частин.
Якщо неможливо розташувати на першому поверсі усі пости ТО і ремонту, то в першу чергу розміщують пости ЩО, Д, ТО-1 як такі, що найбільше відвідуються.
Підрозділ 2.2 «Організація ТО і ремонту автомобілів на робочих постах і спеціалізованих виробничих дільницях» є спеціальним. Розроблення ведеться тільки для одного підрозділу підприємства, поглиблене розроблення якого було обґрунтовано при виконанні техніко-економічного обґрунтування дипломного проекту. Тому в заголовку підрозділу необхідно вказувати назву зони або дільниці, що розробляється.
В 2.2.1 «Характеристика підрозділу» необхідно навести значення і місце підрозділу у загальній схемі технологічного процесу, визначити загальний перелік видів робіт, які виконуються в підрозділі.
В 2.2.3 «Розроблення технологічного процесу робіт у зоні або на дільниці» необхідно розробити загальний технологічний процес виконання робіт в підрозділі. Загальний технологічний процес найдоцільніше надати у вигляді блок-схеми або графу, які відображають перелік та послідовність виконання робіт і визначаються технологічним призначенням зони (дільниці, поста), що проектується. При необхідності розробляється функціональна схема виконання ремонтних робіт, яка показує зв’язки даного виробничого підрозділу з іншими зонами чи дільницями підприємства.
Розроблена загальна технологія повинна визначити весь комплекс робіт, що виконуються в зоні (дільниці, посту), і забезпечити можливість розподілу об’ємів цих робіт по постах і робочих місцях, а також можливість вибору необхідного технологічного обладнання.
В 2.2.4 «Розподіл об’ємів робіт і виконавців на постах, робочих місцях і їх кваліфікації» виконується розподіл трудомісткостей виконання робіт (визначених в пункті 2.1.1) за робочими місцями, які організовуються на дільниці, та визначаються спеціальності і кваліфікація виконавців.
Розподіл об’ємів робіт і виконавців по робочих місцях доцільно виконувати паралельно з вибором технологічного обладнання для зони (дільниці, поста), що проектується. Тобто, необхідно попередньо вибрати основне технологічне обладнання згідно з загальним технологічним процесом, а після розподілу визначити повний перелік технологічного обладнання, оснастки та інструменту.
Розподіл об’ємів робіт і виконавців по робочих місцях зон ТО.
Розподіл проводиться на основі певної кількості постів ТО, вибраного методу організації обслуговування і розробленого загального технологічного процесу в зоні ТО.
Розподіл трудомісткостей робіт по постах зони, що проектується можна проводити за двома ознаками: по-перше – за видами робіт ТО (наприклад: пост № 1 – контрольно-діагностичні, пост № 2 – кріпильні і регулювальні тощо); по-друге – за агрегатами і системами автомобіля (наприклад: пост № 1 – обслуговування двигуна, пост № 2 – агрегати трансмісії тощо). Можливий змішаний варіант розподілу, тобто: розподіл проводиться за агрегатами автомобіля, а деякі види робіт (як правило діагностичні, мастильні) виносяться на окремий пост. Послідовність проведення розподілу може бути такою.
1. Виходячи з вибраного раніше методу організації технологічного процесу в зоні, що проектується прийняти метод розподілу робіт по постах (1 – за видами робіт, 2 – за агрегатами і системами автомобіля, 3 – змішаний), даючи перевагу другому і третьому. При цьому можна користуватись розробленими типажами зон ТО і ПР.
2. Знаючи кількість постів в зоні, розділити весь обсяг робіт технічного обслуговування по постах зони ТО.
3. Способом розподілу трудомісткостей ТО і ПР поділити кожний пост на кілька робочих місць, і визначити, які роботи будуть проводитись на кожному робочому місці і в якому об'ємі.
4. Виходячи з об'єму робіт, визначити розрахункову кількість робочих на кожне робоче місце (аналогічно визначенню чисельності робочих для цілої зони ТО).
5. Групуючи трудомісткості виконання різних робіт, добитись, щоб кількість виконавців на робочих місцях була близька до цілого числа. Користуючись тарифно-кваліфікаційними довідниками вибрати необхідні спеціальності і розряди робочих.
Розподіл об’ємів робіт і виконавців по робочих місцях зони ПР.
Розподіл трудомісткостей і виконавців по постах і робочих місцях зони ПР проводиться аналогічно розподілу об'ємів робіт з ТО, з врахуванням таких особливостей.
1. Для виконання поточного ремонту на постах ПР не застосовується метод ремонту на поточних лініях.
2. При виконанні ПР на універсальних постах необхідно визначити частку загального об'єму постових робіт ПР, яка припадає на один типовий (універсальний) пост і провести в межах цього поста розподіл об’ємів робіт і виконавців по робочих місцях. Всі інші пости вважаються аналогічними.
3. При виконанні ПР на спеціалізованих постах, розподіл по постах зони проводиться, в основному, за агрегатами і системами автомобіля (як виключення, можливе проведення деякого виду робіт по цілому автомобілю на окремому посту (контрольно-діагностичні, малярні). Частка трудомісткостей постових робіт, яка припадає на окремий агрегат чи систему автомобіля, визначається за [20, 24, 25, 28, 29].
Розподіл об’ємів робіт і виконавців по робочих місцях дільниць ПР.
При проектуванні дільниць ПР розподіл об’ємів робіт проводиться в межах тільки цієї дільниці по робочих місцях. При цьому необхідно врахувати, що один робочий може працювати на декількох робочих місцях.
Розподіл можна проводити в такій послідовності.
1. Користуючись типовими плануваннями дільниць ПР, на основі розробленого загального технологічного процесу, виконати попереднє планування дільниці з розташуванням вибраного технологічного обладнання.
2. За попереднім плануванням дільниці визначити кількість і місця розташування робочих місць на ній.
3. Знаючи загальний об’єм і технологію проведення робіт на дільниці, визначити, які роботи і в якому об’ємі будуть виконуватись на кожному робочому місці.
4. Виходячи з об’єму робіт, визначити розрахункову кількість робочих на кожне робоче місце (аналогічно визначенню чисельності робочих для цілої дільниці).
5. Групуючи трудомісткості виконання різних робіт, домогтись, щоб кількість виконавців на робочих місцях була близька до цілого числа. Користуючись тарифно-кваліфікаційними довідниками вибрати необхідні спеціальності і розряди робочих.
2.2.4 Обґрунтування і вибір технологічного обладнання доцільно виконувати на основі варіантного пошуку, порівнюючи кілька варіантів технологічного обладнання між собою на основі технічних та вартісних показників.
Технологічне обладнання – це оснастка виробничих зон АТП і СТОА, призначенням якої є механізація технологічних процесів технічного обслуговування і ремонту рухомого складу автомобільного транспорту.
Обладнання для проведення робіт на постах зон ТО, ПР, діагностики, а також для дільниць і цехів АТП, приймається відповідно до технологічної необхідності, виходячи з умов забезпечення технологічного процесу виконання робіт з ТО або ПР.
При виконанні дипломного проекту все обладнання необхідно поділити на три групи:
– основне технологічне обладнання (станки, стенди, діагностичне, підйомно-оглядове, підйомно-транспортне тощо);
– технологічну оснастку (верстаки, столи, шафи, стелажі тощо);
– пристрої та інструменти (спеціальні пристрої, спеціалізовані комплекти інструментів, універсальні інструменти тощо).
Номенклатура і кількість обладнання виробничих зон і дільниць приймаються за табелями і довідниками технологічного обладнання і спеціалізованого інструменту для АТП і СТОА [41, 42, 44, 45].
Кількість основного технологічного обладнання визначається за річною трудомісткістю робіт на цьому обладнанні:
, (5.79)
де
– річний об’єм даного виду робіт;
– кількість робочих днів зон ТО і ПР;
– тривалість робочої зміни;
– число змін;
– коефіцієнт використання обладнання, відношення часу роботи обладнання до тривалості робочої зміни. Коефіцієнт залежить від роду і призначення обладнання. В умовах АТП він може бути рівним 0,75 ... 0,9.
– число робітників, одночасно працюючих на даному обладнанні.
Кількість обладнання, яке використовується періодично, тобто немає повного завантаження, визначається комплектом за типовим табелем обладнання для даної дільниці, зони, поста в залежності від кількості автомобілів на підприємстві.
Число одиниць піднімально-оглядового обладнання визначається числом постів ТО і ПР та ступеня механізації технологічних процесів в зонах і дільницях ТО і ПР.
Кількість технологічної оснастки визначається залежно від числа робітників, що працюють в найбільш завантажену зміну.
При визначенні кількості верстаків та робочих столів необхідно врахувати кількість робітників в найбільш завантажену зміну, які будуть за ними працювати.
При визначенні кількості тумбочок і шаф для пристроїв та інструментів, а також кількості стелажів для агрегатів і запасних частин необхідно врахувати зручність доступу до них і кількість агрегатів, запасних частин, пристроїв та інструментів, що будуть на них зберігатися.
Кількість спеціальних пристроїв та комплектів інструментів вибирається залежно від числа робочих, які будуть працювати з цим інструментом.
Приклад. Визначимо кількість стендів для розбирання-складання двигунів на дільниці для ремонту двигунів.
Згідно з розподілом об’ємів робіт і виконавців трудомісткість цього виду робіт складає 3800 (люд.-год) і число виконавців два. Одночасно біля стенду може працювати один робочий.
.
Приймаємо два стенди.
За результатами вибору технологічного обладнання формується табель технологічного обладнання за формою табл. 5.42.
Таблиця 5.42 – Табель технологічного обладнання _________ дільниці (зони)
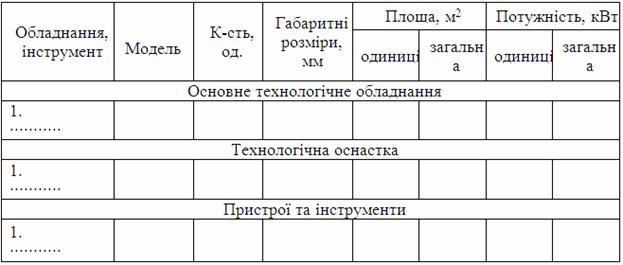
Сумарна площа